Team Associated TC6 Thread
#9047

anyone know what i should gear my tc6.1 for 17.5? i have a mach 2.
looking for gearing tips for 64p and 48p.
thanks.
looking for gearing tips for 64p and 48p.
thanks.
#9050

sorry if this has already been noted and/or fix to what I see is a design flaw. Forgive me as I'm new to the TC6, but the main problem I see is the risk for the motor to easily lose its mesh setting during heavy track rubbing or hitting a flapper too hard in a chicane. I'm going to experiment with some "Amazing Goop" glue and fill the gap between the motor screw and the forward area of the motor mount. The glue is rated to withstand temperatures up to 150° so I may have to install a fan to keep temps within range. Main reason why I want to use Amazing Goop is that it will be easy to remove when the time comes to change my gear ratio.
If someone has a better idea to overcome this design flaw, please share, thanks!
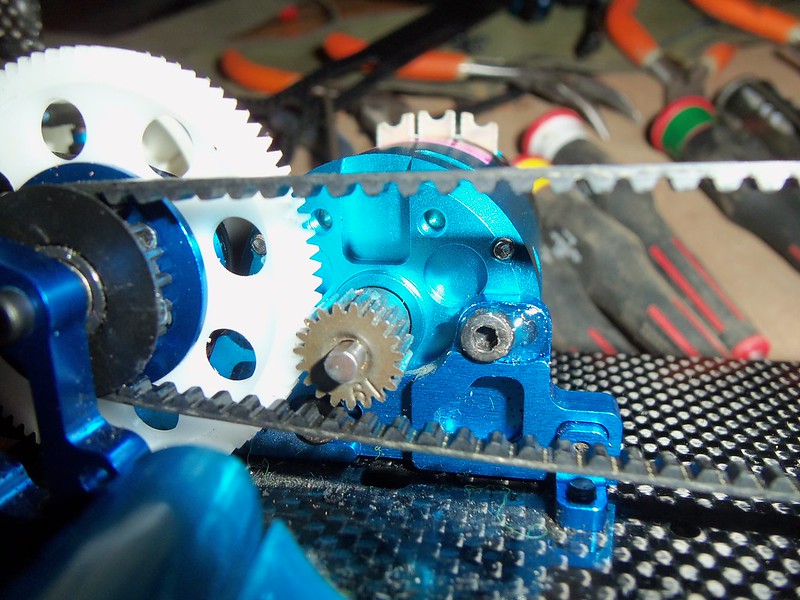
Most cars I've raced in the past have the adjustment slots at an angle to minimize losing the mesh setting, this motor mount is in a perfect parallel line with the chassis, oops!
If someone has a better idea to overcome this design flaw, please share, thanks!
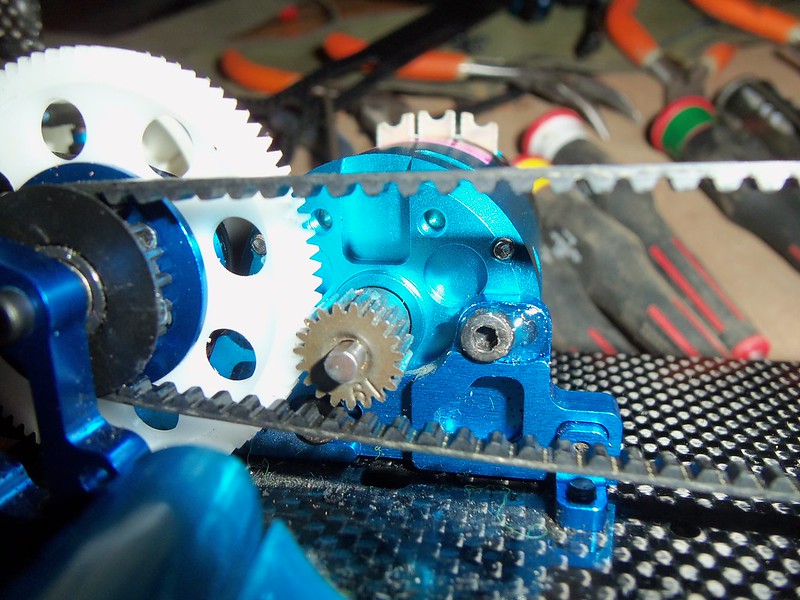
Most cars I've raced in the past have the adjustment slots at an angle to minimize losing the mesh setting, this motor mount is in a perfect parallel line with the chassis, oops!
#9051

sorry if this has already been noted and/or fix to what I see is a design flaw. Forgive me as I'm new to the TC6, but the main problem I see is the risk for the motor to easily lose its mesh setting during heavy track rubbing or hitting a flapper too hard in a chicane. I'm going to experiment with some "Amazing Goop" glue and fill the gap between the motor screw and the forward area of the motor mount. The glue is rated to withstand temperatures up to 150° so I may have to install a fan to keep temps within range. Main reason why I want to use Amazing Goop is that it will be easy to remove when the time comes to change my gear ratio.
If someone has a better idea to overcome this design flaw, please share, thanks!
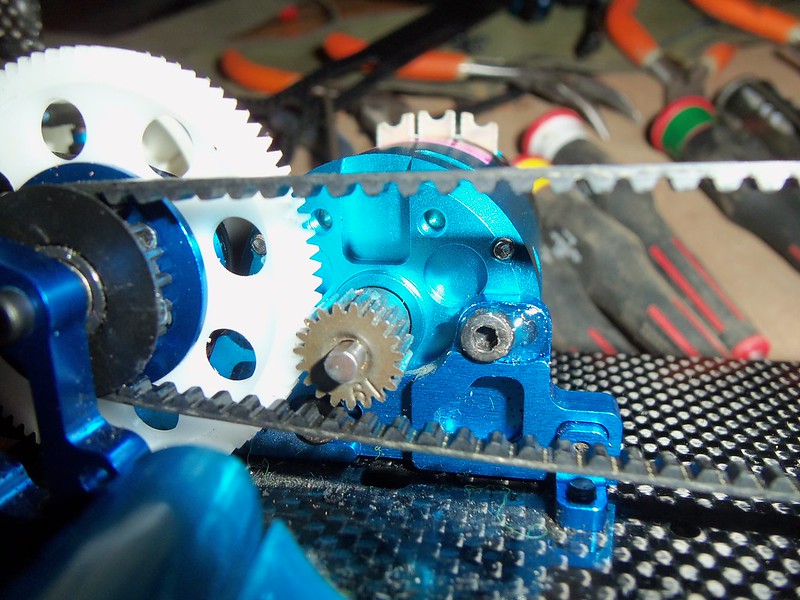
Most cars I've raced in the past have the adjustment slots at an angle to minimize losing the mesh setting, this motor mount is in a perfect parallel line with the chassis, oops!
If someone has a better idea to overcome this design flaw, please share, thanks!
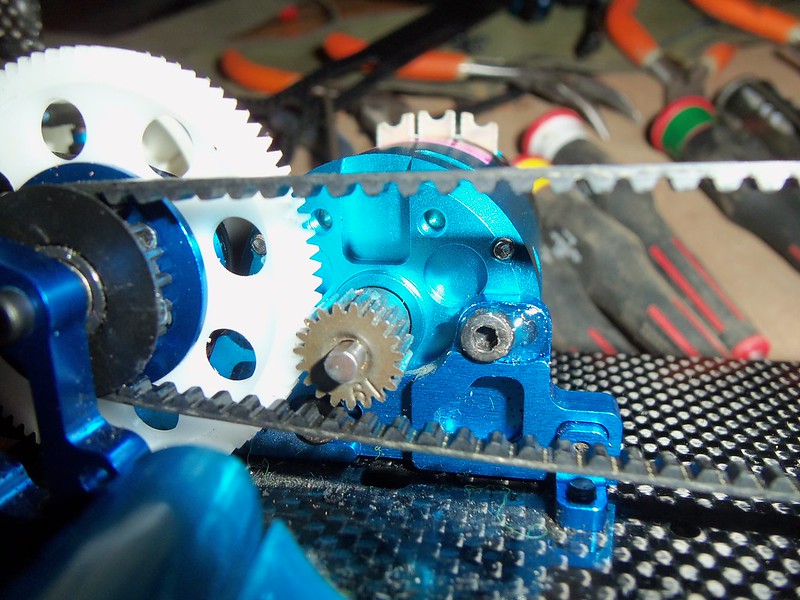
Most cars I've raced in the past have the adjustment slots at an angle to minimize losing the mesh setting, this motor mount is in a perfect parallel line with the chassis, oops!
Well, you can only consider this a design flaw if the majority of users are having the same problem. If it's an isolated case, it is either a manufacturing defect or user error. Sure, having the slot angled may be a better approach but that doesn't make the current design a "flaw" By any means.There may be reasons for associated's approach on this. Either way, I am working on a 1 piece motor mount/spur mount that will change this design for the better I think.

Lets also consider that hitting other objects on the track is not considered "normal" operating conditions.

I for one, have never had my motor move when properly tightened on either of my TC6's and I'm only using 2 screws.
#9052

I have wacked many things with mine.... The motor nevered moved, other things have ( servotape on esc and reciever let go.) but never the motor. If its moving i think it isn't tight enough.
#9053
Tech Rookie

The motor mount washers from the tc5r part # ASC9630 with blue tamiya gel threadlock will do the trick. There ballstud washers but when you tighten the motor screws hard they basically crush and that baby wont budge.
#9056


I've worked with Amazing Goop before and it peels away from aluminum with semi-medium effort which seems to be the appropriate product for this application. I'm not so sure a plastic shim will stay in place without a captured backing.
Hopefully the cases I've seen on the track were all isolated and had nothing to do with the design of the car but merely loose screws because the drivers didn't use any thread lock. I didn't ask each driver if they had used any thread lock or not.
#9057
Tech Addict
iTrader: (21)

That's interesting, Bill. But, FWIW, that's basically the same motor mounting method that's been used on most cars since I started racing in the '80s. I do know some folks had issues with the Axial motors shifting, but that's more of an issue with the motor can itself. I still don't think it's anything to worry about, but I understand your reasoning...
#9058
Tech Adept

I've seen at least 3 local drivers have problems losing their mesh after hard hits on the track and I never got a really close look into the root of the problem until now. If the glue fails to hold up to the heat, and I experience the same issue as I've seen other drivers suffer from, then I plan to use my plastic welder which should theoretically form a reusable shim to fill the void. perhaps I could make several shims for varying mesh combinations 
I've worked with Amazing Goop before and it peels away from aluminum with semi-medium effort which seems to be the appropriate product for this application. I'm not so sure a plastic shim will stay in place without a captured backing.
Hopefully the cases I've seen on the track were all isolated and had nothing to do with the design of the car but merely loose screws because the drivers didn't use any thread lock. I didn't ask each driver if they had used any thread lock or not.

I've worked with Amazing Goop before and it peels away from aluminum with semi-medium effort which seems to be the appropriate product for this application. I'm not so sure a plastic shim will stay in place without a captured backing.
Hopefully the cases I've seen on the track were all isolated and had nothing to do with the design of the car but merely loose screws because the drivers didn't use any thread lock. I didn't ask each driver if they had used any thread lock or not.
And that's when I first got it over 1 and half ago
Is a brillant solid car
#9059

It was pointed out to me via PM that the problem with the design is only for folks using brushed motors (in a spec class) which only has 2 threaded holes directly opposite from each other on the can, then if you don't have an open slotted spur, it's nearly impossible to tighten the screw closest to the rear diff because the screw is blocked by a solid plastic spur (I think this is what Tommy was trying to explain earlier). Those drivers were at the mercy of only one properly tightened screw, unless they painfully guessed several screw settings while removing the spur and tightening the screw behind with each successive guess.
Why not have a motor mount that fully encloses a circle around the shaft of the motor and have angled slots above and below such that there is no interference from the spur? Or at least raise the front hole so that it's directly opposite from the bottom hole. Those with brushless motors can get away with the current design because there are plenty of extra pre drilled holes in most brands of brushless motors.
Another argument can be made that brushed motors are going to soon be extinct anyway so why bother making a product backward compatible? Or simply buy a spur with super size holes to get to that rear screw.... I digress.
I'm just happy to learn I shouldn't expect any problems since I'm running a brushless motor, thanks everyone
Why not have a motor mount that fully encloses a circle around the shaft of the motor and have angled slots above and below such that there is no interference from the spur? Or at least raise the front hole so that it's directly opposite from the bottom hole. Those with brushless motors can get away with the current design because there are plenty of extra pre drilled holes in most brands of brushless motors.
Another argument can be made that brushed motors are going to soon be extinct anyway so why bother making a product backward compatible? Or simply buy a spur with super size holes to get to that rear screw.... I digress.
I'm just happy to learn I shouldn't expect any problems since I'm running a brushless motor, thanks everyone

#9060

It was pointed out to me via PM that the problem with the design is only for folks using brushed motors (in a spec class) which only has 2 threaded holes directly opposite from each other on the can, then if you don't have an open slotted spur, it's nearly impossible to tighten the screw closest to the rear diff because the screw is blocked by a solid plastic spur (I think this is what Tommy was trying to explain earlier). Those drivers were at the mercy of only one properly tightened screw, unless they painfully guessed several screw settings while removing the spur and tightening the screw behind with each successive guess.
Why not have a motor mount that fully encloses a circle around the shaft of the motor and have angled slots above and below such that there is no interference from the spur? Or at least raise the front hole so that it's directly opposite from the bottom hole. Those with brushless motors can get away with the current design because there are plenty of extra pre drilled holes in most brands of brushless motors.
Another argument can be made that brushed motors are going to soon be extinct anyway so why bother making a product backward compatible? Or simply buy a spur with super size holes to get to that rear screw.... I digress.
I'm just happy to learn I shouldn't expect any problems since I'm running a brushless motor, thanks everyone
Why not have a motor mount that fully encloses a circle around the shaft of the motor and have angled slots above and below such that there is no interference from the spur? Or at least raise the front hole so that it's directly opposite from the bottom hole. Those with brushless motors can get away with the current design because there are plenty of extra pre drilled holes in most brands of brushless motors.
Another argument can be made that brushed motors are going to soon be extinct anyway so why bother making a product backward compatible? Or simply buy a spur with super size holes to get to that rear screw.... I digress.
I'm just happy to learn I shouldn't expect any problems since I'm running a brushless motor, thanks everyone

http://www.rctech.net/forum/electric...ts-thread.html