HPI R40 Nitro Car Forum
#5311

hey guys,
I finally got my r40 started today awhere it would run decient. I should have knew this would happen but, the idle and clutch engagement are off. Its hard for me to really tell. I lowered the idle sped, but that didnt help me. I think it is the clutch engagement. How do I make the clutch engage LATER? Is it left or right on the clutch nut?
Thanks,
Don
P.S. I also think I am going to take the one way diff out untill I can make out the way it handles.
I finally got my r40 started today awhere it would run decient. I should have knew this would happen but, the idle and clutch engagement are off. Its hard for me to really tell. I lowered the idle sped, but that didnt help me. I think it is the clutch engagement. How do I make the clutch engage LATER? Is it left or right on the clutch nut?
Thanks,
Don
P.S. I also think I am going to take the one way diff out untill I can make out the way it handles.
#5312

I reliazed that more spacers the better. Try using 4 in this combo: Silver, copper, silver, copper. I did that and the clutchbell doesn't push out as much, which will allow the clutch shoe to hit the flywheel and move the car. Once I did this and adjusted the adjuster nut the car hauls ass seriously. I underestimated the MT12, but now that I seen what it can do I'd rather keep it the way it is and run it. The car hauls ass soo much than even when my friend ran his r40 with Rody 3 port engine (he skipped break in a lil and just ran it around a bit) I totally nailed him. This engine has so much power though now it seems top end is a lil under. No problem, because I have my ride to shift into 2nd on 2 seconds flat while it's revving at it's best so it hauls big time. Another friend came and ran his NTC3 and we both ended up with damage to the spur thnx to a heap of pebbles. A big rock scratched up his driveshaft and one got stuck between the flywheel and chassis causing it to shut off. Other than that, the car was running awesome and hauled it's ass off big time. Many thnx to a lil tuning of mine in the bathroom earlier with the clutch and actually starting it to see how she ran. This thing totally rocks. Now my decision is to get few more parts for the car and get the .27 engine for my MGT so I can run this bad boy.
SShhheweeettttttt!!!



#5313

I have a chassis saver I used on mine. It is made from HDPE and it is about 2 - 3 mm thick originally. You can grind it down to 1 - 2 mm.
Basically, I cut a piece of this material and drilled two holes so that it can be placed at the very rear of the underside of the chassis and you simply used the bottom rear chassis screws to hold it in place (countersunk screw holes required).
Actually any material could have been used I just had some laying around.
You get the idea.
Basically, I cut a piece of this material and drilled two holes so that it can be placed at the very rear of the underside of the chassis and you simply used the bottom rear chassis screws to hold it in place (countersunk screw holes required).
Actually any material could have been used I just had some laying around.
You get the idea.
#5314

Originally posted by regg151
did anyone ever find a soloution to stop the rear links from compressing?
I recall someone getting some nuts machined to fit but was there any other way?
did anyone ever find a soloution to stop the rear links from compressing?
I recall someone getting some nuts machined to fit but was there any other way?
One thing for sure - "when you do compress ;you must replace". That was my tribute to Johnny C. for what it's worth.
I had a few ideas when I was tackeling this issue -
- use heli-coils in the plastic ends ( if you can find LHT)
- convert over to a 5mm turnbuckle ( might require extensive research.
Basically, the flaw is in the strength of the plastic ends. You never know, once you beef the plastic ends up you might create another "weak link" in the system. Just experiment.
Let us know what you come up with.
#5315

I was actually contemplating useing a small amout of JB weld in the threads and setting up a few sets at varying sizes to maintain some adjutability for track conditions.
I find this to be rather extreme but if it works it would solve the problem.
either that or drill a hole in each plastic arm and install a grub screw to help hold it in place.
ya know that just might work. one way to find out.
I find this to be rather extreme but if it works it would solve the problem.
either that or drill a hole in each plastic arm and install a grub screw to help hold it in place.


#5316

I have had the same problem and found that the quickest and easiest solution was to use the spacers from the front caster adjusters clipped over the threads to stop them from compressing. It's quick and easy no mucking around and still adjustable. You may want to put a metal washer on the turnbuckle either side of the hex first to stop the plastic spacer spreading and pushing up over the hex and allowing compression.
Hope this helps
Hope this helps
#5317

Okay guys, I'll post this info I lifted from early on in this thread again on clutch setup
I have found several things with the clutch.
1. You most likely need to put shims between the inside bearing and the sg nut to keep the bell from rubbing the shoe.
2.Clearance to the chassis cutout for the flywheel, on some of my engines I had to remove the big washer behind the collet other wise the outside of the bell will hit the chassis= slip
This can also happen if the motor is aligned too far to the gear side. I think this has been my problem all along, but in the process I learned the fine points of setting up a Centax.
3. The red clutch shoe as with most cars is better than the slip prone black stuff
If assembled right the clutch is supposed to be great; it's nearly identical to the Mugen's
I was starting to build the clutch last night....and I have to agree, the stock setting of the clutch (per manuel) is not even close to the GOOD setting of the centax..........
(1) I agree with OB42TC3's #1 idea....I ended up put a 0.1mm shim (from Serpent or NTC3 package) behind the SG nut and in front of the first bearing of the clutch housing in order to spin the house freely without rubbing the shoe.
(2) The 0.8mm shims behind the collet need to be increase to close to 1mm (I ended up adding 2 more 0.1mm from Serpent) in order for me to get to 0.3mm gap different....no matter how much or less shims I did in front of the threst bearing, it won't give me the clearence that I like....
Overall....that is the setting that I have on my RS 12 T5 S1 engine...does not necessary work for other engines, but the concept is like that.....at least 3 areas need to add or remove shims instead of only 1 (before the threst bearing like HPI said)
I still think the RED shoes is the one to use....the HPI one is almost like a solid black plasic block....
OB42TC3 already said it....it is the one from DELTA, you can see that on ebay, they are like $12 each. (keyword: Clutch shoe)...but I am sure the MUGEN one are as good...anything but the stock HPI black one....(if you have the chance to get a better shoe)...
the Mugen ones. They basically are made from the same material however, Rulon. The R40 one is absolutely ballistic it makes the car have incredible punch. You can email order them from Delta.
The Grey ones work nicely, but have less punch than the Red shoes, but to get it to slide on the pins properly you will need to ream the holes a bit. I posted a picture of this a few months ago.
If you are running your car at Brendale you should definately get the red ones, the cost me around AUD$15 from Delta. Most other local tracks will be fine with the grey shoes.
I posted this a while ago. Here is my latest clutch setup that has so much punch the car actually was jumping slightly on a low bite track:
Delta Red shoes
Kyosho Bronze colour spring - FW16
A heap of Mugen shims (or any other shims will work)
1. Assemble the clutch without the unner bearing. Pull the clutch housing away from the shoe. Measure the gap between the housing and the shoe. This is the clutch gap. You want it between 0.4-0.6mm in my setup.
2. Put the inner bearing back in place. Add shims between this bearing and the clutch nut until there is almost no float. 0.1mm or less.
3. Set the adjuster nut to 1.4mm.
This setup gives awesome clutch response, and also is far easier on the clutch bearings. I have posted previously that I had bearing failures, I have had no failures since I have been using this setup.
AMG, Thanks for the information, and that is exactly what I want to know...I was playing with SHIMS with the R40 centax, as much as they did a good car like R40, their centax is still not as good as a centax compare to Mugen or Serpent.
I have replaced most of the R40 centax parts with new one (new OEM parts)........I still feel the clutch housing is a little warble here and there..........my 4 years old Serpent centax does not have that kind of a feeling, still spin freely and smoothly.
But anyhow............I still want to work on the R40 centax cause that will fit the R40 the best (I hope), but I want to know, should I stick with the 0.8mm stock black shim behind the collet and add/remove shims in front..?
The old way of building centax is add/remove shim before collet, the newer way of setting centax is FIX shim at the collet and add/remove shim before clutch bearing and in front of the thrust bearing....
And last night, I have to do BOTH........collet shim ended up to 1mm and add a 0.4mm before bearing and 0.8mm before thrust bearing............STILL.........ended up 0.45mm gap different, which I don't really satisfried with, I want to shorted it to 0.25mm to 0.35mm range.....which is very easy to set on all of my Serpent Centax.
This is by far the longest time I have to spend on doing a Centax system.
quote:
Originally posted by Rookie Solara
Also, do you guys know that the thrust bearing from the R40 centax, both O-RING are having different inner diameter just like Serpent or Mugen Thrust bearing....? And the larger diameter one are suppose to go in first (toward flywheel) and the smaller diameter one are facing outside.
Thrust bearings ALWAYS have one ring with bigger inner diameter than the other and you always need to put the bigger inner diameter first towards the clutch shoes and then the smaller one further out.
quote:
Originally posted by Rookie Solara
I didn't see HPI manual mentioned that, don't know that matters or not, but on Serpent and Mugen's manuel, they both mentioned it and it must go in to the right direction.
If you did not happen to install the thrust bearing right, then HPI just gets richer selling blown out thrust bearing replacements.
quote:
Originally posted by Proteus
It's to adjust the roll center for the front upper arms. If you noticed that your kit came with two of those. They are to control the height of the rear portion of the front upper arm. Also, the kit came with two different rubber grommetts (sp?); the piece that fits into the bottom of the shock tower which holds the front upper arm hingepin. With the two different rubber pieces....you have three different positions where you can mount your arm, stock (low), center, and high. Use the corresponding rear pices to adjust the upper hingepin to keep the hingepin parallel to the lower hingepin. Hopefully that makes sense. And there you have it. I've tried raising the roll center by adding one rear shim plus using the other rubber piece. The car felt quite responsive but had no grip. I also tried angling the upper arm as I was using kickup on the lower arm. I ended up going back to the low roll center. That seemed to give me the most traction. I guess on high bite tracks where traction rolling is a problem, using a higher roll center up front would help. AND THERE YOU HAVE IT.
Now I can finally.......
Thanks bubba!!!!
OK I got serious last night and took TQ with my porky 1850g car. Then I broke the car in the first lap of the final. Oh well.
Anyway I learned a few things along the way..........
The clutch fix. The way to make the clutch awesome is as follows:
1. Get a Mugen grey shoe or a Red rulon shoe from Delta. This will eliminate most of the slipping. The stock black shoe I estimates slips around 10000 rpm at least. With the red or grey that drops to a few thousand. Very noticable punch increase.
2. I finally trialled the new spring. I am using the Kyosho hard black spring from the Evolution. A Mugen silver will work similarly. The main advantage is that these springs have less winds and you dont need to crank down on them so hard. They are around 1mm shorter. With the HPI spring you need to crank down on it so hard to get good high engagement you start to get spring bind (the loops touch each other) and the engagement sticks. A harder spring wont get the binding.
I also used a RB V12 motor, still running in. Man this thing was like having a turbocharger on the mid range. The low end was great, but mid range was phenominal!! Top end is less than a NS12, but I did not give up any car speed at all, and I was slightly undergeared as well. I should have my 2004 parts soon............
I have found several things with the clutch.
1. You most likely need to put shims between the inside bearing and the sg nut to keep the bell from rubbing the shoe.
2.Clearance to the chassis cutout for the flywheel, on some of my engines I had to remove the big washer behind the collet other wise the outside of the bell will hit the chassis= slip
This can also happen if the motor is aligned too far to the gear side. I think this has been my problem all along, but in the process I learned the fine points of setting up a Centax.
3. The red clutch shoe as with most cars is better than the slip prone black stuff
If assembled right the clutch is supposed to be great; it's nearly identical to the Mugen's
I was starting to build the clutch last night....and I have to agree, the stock setting of the clutch (per manuel) is not even close to the GOOD setting of the centax..........
(1) I agree with OB42TC3's #1 idea....I ended up put a 0.1mm shim (from Serpent or NTC3 package) behind the SG nut and in front of the first bearing of the clutch housing in order to spin the house freely without rubbing the shoe.
(2) The 0.8mm shims behind the collet need to be increase to close to 1mm (I ended up adding 2 more 0.1mm from Serpent) in order for me to get to 0.3mm gap different....no matter how much or less shims I did in front of the threst bearing, it won't give me the clearence that I like....
Overall....that is the setting that I have on my RS 12 T5 S1 engine...does not necessary work for other engines, but the concept is like that.....at least 3 areas need to add or remove shims instead of only 1 (before the threst bearing like HPI said)
I still think the RED shoes is the one to use....the HPI one is almost like a solid black plasic block....
OB42TC3 already said it....it is the one from DELTA, you can see that on ebay, they are like $12 each. (keyword: Clutch shoe)...but I am sure the MUGEN one are as good...anything but the stock HPI black one....(if you have the chance to get a better shoe)...
the Mugen ones. They basically are made from the same material however, Rulon. The R40 one is absolutely ballistic it makes the car have incredible punch. You can email order them from Delta.
The Grey ones work nicely, but have less punch than the Red shoes, but to get it to slide on the pins properly you will need to ream the holes a bit. I posted a picture of this a few months ago.
If you are running your car at Brendale you should definately get the red ones, the cost me around AUD$15 from Delta. Most other local tracks will be fine with the grey shoes.
I posted this a while ago. Here is my latest clutch setup that has so much punch the car actually was jumping slightly on a low bite track:
Delta Red shoes
Kyosho Bronze colour spring - FW16
A heap of Mugen shims (or any other shims will work)
1. Assemble the clutch without the unner bearing. Pull the clutch housing away from the shoe. Measure the gap between the housing and the shoe. This is the clutch gap. You want it between 0.4-0.6mm in my setup.
2. Put the inner bearing back in place. Add shims between this bearing and the clutch nut until there is almost no float. 0.1mm or less.
3. Set the adjuster nut to 1.4mm.
This setup gives awesome clutch response, and also is far easier on the clutch bearings. I have posted previously that I had bearing failures, I have had no failures since I have been using this setup.
AMG, Thanks for the information, and that is exactly what I want to know...I was playing with SHIMS with the R40 centax, as much as they did a good car like R40, their centax is still not as good as a centax compare to Mugen or Serpent.
I have replaced most of the R40 centax parts with new one (new OEM parts)........I still feel the clutch housing is a little warble here and there..........my 4 years old Serpent centax does not have that kind of a feeling, still spin freely and smoothly.
But anyhow............I still want to work on the R40 centax cause that will fit the R40 the best (I hope), but I want to know, should I stick with the 0.8mm stock black shim behind the collet and add/remove shims in front..?
The old way of building centax is add/remove shim before collet, the newer way of setting centax is FIX shim at the collet and add/remove shim before clutch bearing and in front of the thrust bearing....
And last night, I have to do BOTH........collet shim ended up to 1mm and add a 0.4mm before bearing and 0.8mm before thrust bearing............STILL.........ended up 0.45mm gap different, which I don't really satisfried with, I want to shorted it to 0.25mm to 0.35mm range.....which is very easy to set on all of my Serpent Centax.
This is by far the longest time I have to spend on doing a Centax system.
quote:
Originally posted by Rookie Solara
Also, do you guys know that the thrust bearing from the R40 centax, both O-RING are having different inner diameter just like Serpent or Mugen Thrust bearing....? And the larger diameter one are suppose to go in first (toward flywheel) and the smaller diameter one are facing outside.
Thrust bearings ALWAYS have one ring with bigger inner diameter than the other and you always need to put the bigger inner diameter first towards the clutch shoes and then the smaller one further out.
quote:
Originally posted by Rookie Solara
I didn't see HPI manual mentioned that, don't know that matters or not, but on Serpent and Mugen's manuel, they both mentioned it and it must go in to the right direction.
If you did not happen to install the thrust bearing right, then HPI just gets richer selling blown out thrust bearing replacements.
quote:
Originally posted by Proteus
It's to adjust the roll center for the front upper arms. If you noticed that your kit came with two of those. They are to control the height of the rear portion of the front upper arm. Also, the kit came with two different rubber grommetts (sp?); the piece that fits into the bottom of the shock tower which holds the front upper arm hingepin. With the two different rubber pieces....you have three different positions where you can mount your arm, stock (low), center, and high. Use the corresponding rear pices to adjust the upper hingepin to keep the hingepin parallel to the lower hingepin. Hopefully that makes sense. And there you have it. I've tried raising the roll center by adding one rear shim plus using the other rubber piece. The car felt quite responsive but had no grip. I also tried angling the upper arm as I was using kickup on the lower arm. I ended up going back to the low roll center. That seemed to give me the most traction. I guess on high bite tracks where traction rolling is a problem, using a higher roll center up front would help. AND THERE YOU HAVE IT.
Now I can finally.......
Thanks bubba!!!!
OK I got serious last night and took TQ with my porky 1850g car. Then I broke the car in the first lap of the final. Oh well.
Anyway I learned a few things along the way..........
The clutch fix. The way to make the clutch awesome is as follows:
1. Get a Mugen grey shoe or a Red rulon shoe from Delta. This will eliminate most of the slipping. The stock black shoe I estimates slips around 10000 rpm at least. With the red or grey that drops to a few thousand. Very noticable punch increase.
2. I finally trialled the new spring. I am using the Kyosho hard black spring from the Evolution. A Mugen silver will work similarly. The main advantage is that these springs have less winds and you dont need to crank down on them so hard. They are around 1mm shorter. With the HPI spring you need to crank down on it so hard to get good high engagement you start to get spring bind (the loops touch each other) and the engagement sticks. A harder spring wont get the binding.
I also used a RB V12 motor, still running in. Man this thing was like having a turbocharger on the mid range. The low end was great, but mid range was phenominal!! Top end is less than a NS12, but I did not give up any car speed at all, and I was slightly undergeared as well. I should have my 2004 parts soon............
#5318

Here is a pretty complete list of things to lighten the car.
Someone made a list earlier in this thread, I've modified it a bit:
- Both Hollow shafts #33401 & #33402
- Graphite front and rear shocktowers #73089 & #73090
- Full set of Ti screws (#Z368 for the HPI set, Yokomo also makes machine-thread Ti screws, and you can use aluminum screws in low-stress areas to save some grams)
- Titanium turnbuckles (two 4 x 40mm, two 4-40 x 24mm)
- Super chassis #73924
- Light top deck (#33408, must order from Asia or just remove the receiver box, see below)
- 0.8 module gearbox #87173
- Heat sink engine mount #33405
- Graphite suspension arms (not sure if part # is different, the arms have been updated since initial release - if you have 2 sway bar mounts on the rear arm you have the new arms)
- Titanium pivotballs (#33426 for 2 or #33427 for 8)
- Titanium hingepins (not sure of brand/part #)
- Graphite steering drag plate (not sure of brand/part #)
- Graphite lower front suspension mounts (not sure of brand/part #)
- Graphite side brace #73104 or #73105 (thinner version)
- Lightweight HPI battery (#33410, order from Asia make your own, see below)
- Remove upper battery cover
- Front One-way #75026
- 9550 steering servo, 3003 throttle servo (or any low-profile servos)
- Airtronics (Sanwa) 211 RX or and micro-size receiver
- don't use the aluminum rear brace or upper deck mounts (that's my suggestion)
You can also save 40g by making a battery pack from 5 AAA NiMH batteries in 2 + 3 shape instead of a normal battery pack. Mount in the normal position.
You can also mount the antenna on the upper deck and attach the receiver to the upper deck or main chassis using silicone sealant or fiber strapping tape. This allows you to remove the receiver box.
Use an AMBrc personal transponder instead of a normal hand-out transponder. Instead of the plastic mount, you can use spare Lexan to mount it to the upper deck (might save a few grams if you don't use too much glue to hold it in place) or use silicone windscreen seal to attach it to the lower deck (next to the lightweight battery pack).
Someone made a list earlier in this thread, I've modified it a bit:
- Both Hollow shafts #33401 & #33402
- Graphite front and rear shocktowers #73089 & #73090
- Full set of Ti screws (#Z368 for the HPI set, Yokomo also makes machine-thread Ti screws, and you can use aluminum screws in low-stress areas to save some grams)
- Titanium turnbuckles (two 4 x 40mm, two 4-40 x 24mm)
- Super chassis #73924
- Light top deck (#33408, must order from Asia or just remove the receiver box, see below)
- 0.8 module gearbox #87173
- Heat sink engine mount #33405
- Graphite suspension arms (not sure if part # is different, the arms have been updated since initial release - if you have 2 sway bar mounts on the rear arm you have the new arms)
- Titanium pivotballs (#33426 for 2 or #33427 for 8)
- Titanium hingepins (not sure of brand/part #)
- Graphite steering drag plate (not sure of brand/part #)
- Graphite lower front suspension mounts (not sure of brand/part #)
- Graphite side brace #73104 or #73105 (thinner version)
- Lightweight HPI battery (#33410, order from Asia make your own, see below)
- Remove upper battery cover
- Front One-way #75026
- 9550 steering servo, 3003 throttle servo (or any low-profile servos)
- Airtronics (Sanwa) 211 RX or and micro-size receiver
- don't use the aluminum rear brace or upper deck mounts (that's my suggestion)
You can also save 40g by making a battery pack from 5 AAA NiMH batteries in 2 + 3 shape instead of a normal battery pack. Mount in the normal position.
You can also mount the antenna on the upper deck and attach the receiver to the upper deck or main chassis using silicone sealant or fiber strapping tape. This allows you to remove the receiver box.
Use an AMBrc personal transponder instead of a normal hand-out transponder. Instead of the plastic mount, you can use spare Lexan to mount it to the upper deck (might save a few grams if you don't use too much glue to hold it in place) or use silicone windscreen seal to attach it to the lower deck (next to the lightweight battery pack).
#5319

Originally posted by HarKonnenD
This I noted from the start. Using the stock setup the LW 2speed on first gear wobbled a bit due to a little xtra slack. That spacer included is NOT ENOUGH! There is a small amount of space between the E clip on the 2speed side. For a simple fix, use the washer for glowplugs and install it on the shaft over the included spacer. This will eliminate that wobble. It never caused me a problem before, but now with the clutch engaging properly offline, the gears started shaving a tiny bit. Now, it's perfect!
This I noted from the start. Using the stock setup the LW 2speed on first gear wobbled a bit due to a little xtra slack. That spacer included is NOT ENOUGH! There is a small amount of space between the E clip on the 2speed side. For a simple fix, use the washer for glowplugs and install it on the shaft over the included spacer. This will eliminate that wobble. It never caused me a problem before, but now with the clutch engaging properly offline, the gears started shaving a tiny bit. Now, it's perfect!

#5321

My last note on clutch setup.
Make sure that the locator pins for the clutch shoes arn't rubbing against the inside of the clutch bell. I found that I had to tap the pins further into the flywheel about 1/16" further. I have 4 or 5 flywheels and all of them had the same problem. Maybe HPI has made a running change and shortened the pins a bit.
Make sure that the locator pins for the clutch shoes arn't rubbing against the inside of the clutch bell. I found that I had to tap the pins further into the flywheel about 1/16" further. I have 4 or 5 flywheels and all of them had the same problem. Maybe HPI has made a running change and shortened the pins a bit.
#5322

Originally posted by regg151
I was actually contemplating useing a small amout of JB weld in the threads and setting up a few sets at varying sizes to maintain some adjutability for track conditions.
I find this to be rather extreme but if it works it would solve the problem.
either that or drill a hole in each plastic arm and install a grub screw to help hold it in place.
ya know that just might work. one way to find out.
I was actually contemplating useing a small amout of JB weld in the threads and setting up a few sets at varying sizes to maintain some adjutability for track conditions.
I find this to be rather extreme but if it works it would solve the problem.
either that or drill a hole in each plastic arm and install a grub screw to help hold it in place.


I tried set-screws with no luck. The problem is that the plastic piece is not thick where the set screw is inserted ( not much force can be applied to the turnbuckle in other words ).
#5323

Originally posted by JAG Racing
I tried set-screws with no luck. The problem is that the plastic piece is not thick where the set screw is inserted ( not much force can be applied to the turnbuckle in other words ).
I tried set-screws with no luck. The problem is that the plastic piece is not thick where the set screw is inserted ( not much force can be applied to the turnbuckle in other words ).
although I did find a few nuts left over from another project that fit over the tunbuckles and are exactly 3mm thick. so I tried em out and wouldn't ya know with one nut on and the ends completly compressed it keeps the stock distence of 6mm go figure.
I had to grind the corners off them to make em look a bit less hack but I know my links will never compress past 6mm and I still have some degre of adjustability.
#5324
Tech Elite
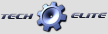
iTrader: (4)
Join Date: Sep 2001
Location: Louisville, KY!.. USA!! ....Home of http://www.fastharry.com
Posts: 2,847
Trader Rating: 4 (100%+)

use PRO LINE tmaxx ends and balls.....use the varying washers from the pro 4 to change roll underneath the rod balls...I used the 23mm lunsford buckles....the stock HPI 20 mm were fine...
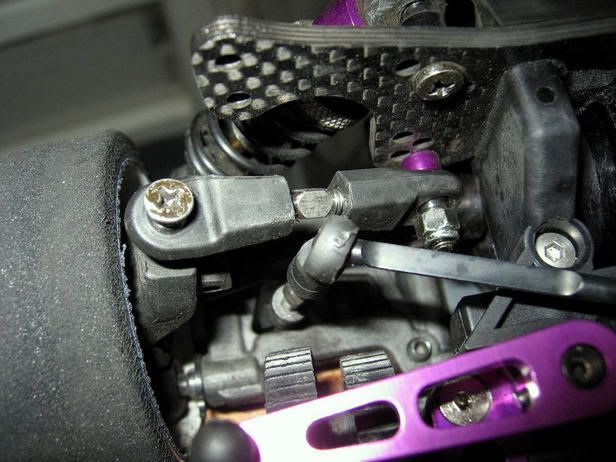
#5325

Ahh now that looks promising, just one questin varying washers??
is this some strange part or just different sized washers (thickness)?
