Tamiya TRF415

I accidentally over tightened a couple of screws on the bottom of my chassis & when I tried to remove them the (2mm) Allen key just keep slipping & rounded them off now I can't access the inner parts like the belt etc to perform maintenance! Therefore my question is what’s the best way to get them out? Will I have to drill them out?

Tech Regular
iTrader: (2)

there are a few technics, take a dremel cutting wheel and cut a slot, ya, you are going to cut the chassie a little. then when you remove the screw, with a flat blade screw driver, then take ca glue and lightly coat the chassie where the screw came out from. let dry when you replace the screw dont use to much torque. the you will be able to remove the screw next time. i bought an xray from a guy who never did the glue thing to the chassie, and every screw needed to be sloted to be removed, man did that suck!
good luck with your screws
good luck with your screws
Tech Elite
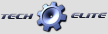
iTrader: (31)
Join Date: Mar 2005
Location: Asphalt Unlimited Customs, Baltimore MD
Posts: 3,144
Trader Rating: 31 (100%+)

do not use a full-sized cut off wheel. i'm going through the same thing with thread locker. Take a pair of snips and cut the cutoff wheel down to half size, then take a grinding stone and shape it down to a 4mm radius.

Originally Posted by jakster
there are a few technics, take a dremel cutting wheel and cut a slot, ya, you are going to cut the chassie a little. then when you remove the screw, with a flat blade screw driver, then take ca glue and lightly coat the chassie where the screw came out from. let dry when you replace the screw dont use to much torque. the you will be able to remove the screw next time. i bought an xray from a guy who never did the glue thing to the chassie, and every screw needed to be sloted to be removed, man did that suck!
good luck with your screws
good luck with your screws
Tech Elite
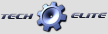
iTrader: (31)
Join Date: Mar 2005
Location: Asphalt Unlimited Customs, Baltimore MD
Posts: 3,144
Trader Rating: 31 (100%+)

yes, that's what is meant. but make sure you read my last post.

HotrodHopkins, I'm afraid I understand yours even less! Not having or ever having used a dremel probably dosen't help. but you say cut the blade inhalf to 4mm does this mean you start with a 8mm? can't you just buy 4mm's. Also if you cut it wont it not be round, is that what the grinding stone is for? Also because of the countersink screw head won't you cut the chassis?
sori to bagger you like this but i am devastated as i've only just bourght it!
sori to bagger you like this but i am devastated as i've only just bourght it!
Tech Regular
iTrader: (2)

ok i will try to make this make sence. use a small round cut off wheel, you are going to cut the chassie just a little where the screw is in the chassie. then use a small bladed screw driver to remove. i wish i was there i could do this faster than it took me to write this. then take ca and q tip and coat lightly the counter sunk hole with ca, let dry. now the screw wont bind on the carbon fiber of the chassie, does that make sence now???

Timbo, first thing you should do is buy a good Hudy 2mm wrench. Now as far as the stripped screw holes go. If you don't want to cut into your chassis, you can try this. It's worked for me in the past. It will require you to dissassemble part of you car. If the stripped screws are not on the same bulkhead, remove all all the bottom screws from the bulkhead so that only the stripped screw is left. Remove everthing on top of the chassis so only the one half bulkhead is left. Turn the bulkhead counter-clockwise. That should loosen the screw. You should still be able to get enough traction with a good wrench to unscrew it from there. Before you put a new screw back in, put a thin layer of CA in the countersunk holes on the chassis. It will keep the screws from sticking. Also, aluminum screws will fuse into the bulkheads. Use titanium or steel screws

Originally Posted by DOTMAN
Timbo, first thing you should do is buy a good Hudy 2mm wrench. Now as far as the stripped screw holes go. If you don't want to cut into your chassis, you can try this. It's worked for me in the past. It will require you to dissassemble part of you car. If the stripped screws are not on the same bulkhead, remove all all the bottom screws from the bulkhead so that only the stripped screw is left. Remove everthing on top of the chassis so only the one half bulkhead is left. Turn the bulkhead counter-clockwise. That should loosen the screw. You should still be able to get enough traction with a good wrench to unscrew it from there. Before you put a new screw back in, put a thin layer of CA in the countersunk holes on the chassis. It will keep the screws from sticking. Also, aluminum screws will fuse into the bulkheads. Use titanium or steel screws
Tech Regular
iTrader: (2)

yes that works also thats if you can get the other side to come free. but you get the idea!

Originally Posted by TacticalTimbo
1 - you say cut the blade inhalf to 4mm does this mean you start with a 8mm? can't you just buy 4mm's.
2- Also if you cut it wont it not be round, is that what the grinding stone is for?
3 - Also because of the countersink screw head won't you cut the chassis?
2- Also if you cut it wont it not be round, is that what the grinding stone is for?
3 - Also because of the countersink screw head won't you cut the chassis?
Basically the cutoff wheel is way bigger than the distance across your screw head so would overlap the screw and cut into your chassis too. To prevent this, you have to trim the cutoff disc down to a size that allows you to cut a slot into the screwhead without overlaping the edges and touching the chassis.
2 - Grinding stone used to make it round after youve trimmed the excess.
3 - No because you only need to cut a slot 1mm or so deep into the screw to allow you to use a flat blade screwdriver to remove it. And youve trimmed the cut off wheel enough already so it will not touch the chassis!
Hope this helped!
Tech Regular
iTrader: (2)

and yes get a 2mm hudy its the tightest tolerance i have used. when every wrench slips, go hudy!

Originally Posted by JAY_UK
1 - Cutoff wheels i believe are only available in one size which is bigger than 4mm.
Basically the cutoff wheel is way bigger than the distance across your screw head so would overlap the screw and cut into your chassis too. To prevent this, you have to trim the cutoff disc down to a size that allows you to cut a slot into the screwhead without overlaping the edges and touching the chassis.
2 - Grinding stone used to make it round after youve trimmed the excess.
3 - No because you only need to cut a slot 1mm or so deep into the screw to allow you to use a flat blade screwdriver to remove it. And youve trimmed the cut off wheel enough already so it will not touch the chassis!
Hope this helped!
Basically the cutoff wheel is way bigger than the distance across your screw head so would overlap the screw and cut into your chassis too. To prevent this, you have to trim the cutoff disc down to a size that allows you to cut a slot into the screwhead without overlaping the edges and touching the chassis.
2 - Grinding stone used to make it round after youve trimmed the excess.
3 - No because you only need to cut a slot 1mm or so deep into the screw to allow you to use a flat blade screwdriver to remove it. And youve trimmed the cut off wheel enough already so it will not touch the chassis!
Hope this helped!
Thankyou so much
Just 1 more Q when looking for the blades i stumbled accross a webpage saying that they shouldn't be used with metal and that it could be dangerous is this true?

Originally Posted by TacticalTimbo
Thankyou so much
Just 1 more Q when looking for the blades i stumbled accross a webpage saying that they shouldn't be used with metal and that it could be dangerous is this true?
Just 1 more Q when looking for the blades i stumbled accross a webpage saying that they shouldn't be used with metal and that it could be dangerous is this true?


so Jay UK what radius should I cut the blade to?