Motor timing and timing curves
#31
Tech Master

the best timing is timing that moves continuously with rpm. there is 1 timing point that generates maximum torque for every rpm. as the rpm goes up or down the timing must do the same if you want peak torque.
so we understand a point on the power curve but there are 20k point on a curve. if if the timing was perfect at 10000 then the motor will be faster at 11000 than it would be if the timing was a little off at 10k. so the previous perfect timing is additive to the next rpm. So the entire 20k points are effected by the previous rpm or the previous timing. so then you might think that you can add .5 degrees per 1000 rpm and that will get you perfect timing. unfortunately it doesnt work that way. at low rpm big changes in timing make very small changes in efficiency. at medium rpm you might need to add 1 degree per 1000 and if all of this is close enough you might need to add 2 degrees of timing per 1000rpm (just example numbers). The point is there are 2 knees in the timing curve and the accuracy of the previous knee effect the results in the subsequent knee. I just go really descriptive about those knees for the sake of understanding. But you could also just set the end bell to handle low rpm, boost to handle mid and turbo to handle high rpm. and if you spend enough time with it you can take a motor that peaks at 150 watts to 300 easily and it will be cooler.
so what happens if the timing isnt right or perfect for that rpm? what happens isnt bad or good. its just something to understand so that you can use it for good or minimize the bad. for every timing point that is not right for an rpm the motor doesnt accelerate as quickly so it doesnt add torque to the next point. secondly the current that should be used to accelerate the motor but cannot be used because the timing isnt right gets turned into heat. the further off the timing is from perfect the more heat. thirdly, because the electrical power moving the rotor isnt right the power that comes back from the motor between pulses isnt right. motors generate electrical power in between the pulses that power the motor. as rpm goes up the electrical power they generate goes higher. at some point the 8.2 volts you are pushing to a motor is matched by 8.2 volts being generated between pulses by the motor and the motor goes no faster. that is max rpm. I had to explain this concept so you can understand what happens when timing isnt right. if the timing isnt right, its said the field is weak. intentionally or accidentally weakening the field is called field weakening. so if the electrical pulse that pushes the rotor forward is weak then the power generated between pulses is weak. so it takes longer for the forward electrical power of 8.2 volts to match the backwards electrical power (generated back emf) and the motor can spin faster. it will do it with least torque but it will spin faster. it will generate more heat but it will spin faster.
so the moral of the story is you never want to weaken the field if you can gear the car and load to match the mechanical power generated with perfect timing. some motors have peak power at 10k some at 15 and some at 20. if you have a track that takes 60 seconds to do a lap you want the average rpm to be at that motors peak rpm. obviously the motor starts at 0 and ends at 20k (example). if the motor constantly accelerates over 60 seconds you want a motor that has perfect timing at 10k and timing that matches. these numbers are exaggerations. the only time you would get something out of field weakening is if your motor has peak power at 10k and you cant gear it to get an average of 12k that the track needs based on its length. in that case you would take away peak power by advancing the timing to weaken the field so that it will average 12k. the only way you get an advantage from field weakening is if you get a wider powerband (not peakier) and this usually only happens if you dont have a motor that has peak power at 12k and you cant get enough gearing into the car to match the average peak power of the motor to match the average peak power the track needs.
a motor manufacturer can give you a set of numbers for that specific motor that takes into account current like 6 amps and a kv number and a timing number that gets you close to that specific motors peak power and you can apply it in a way that minimizes heat and maximizes power but its for a specific motor but you cannot apply it to all motors. every motor has a different resistance. if 1 motor has a different resistance than another then the 8.2 volts going to the motor will match the rpm at which 8.2 volts generated by the motor at a different time and max rpm will be different.
the best way to figure all of this out if you dont have a set of numbers form the mfg and you dont have a dyno is to watch your time per lap. get it as good as you can with gearing. then adjust the timing to minimize heat. if you cant run a race without over heating gear the car to turn 1000 rpm more and adjust the timing again.
every rpm on the curve generates some ratio of torque and heat. the beginning and end of the curve (low and high rpm) generates more heat than mechanical power. bad timing only creates more heat than mechanical power. so you can widen the curve (if that helps) with field weakening or you can use the gearing and timing by lap time to set the motor to the peak power rpm average.
so we understand a point on the power curve but there are 20k point on a curve. if if the timing was perfect at 10000 then the motor will be faster at 11000 than it would be if the timing was a little off at 10k. so the previous perfect timing is additive to the next rpm. So the entire 20k points are effected by the previous rpm or the previous timing. so then you might think that you can add .5 degrees per 1000 rpm and that will get you perfect timing. unfortunately it doesnt work that way. at low rpm big changes in timing make very small changes in efficiency. at medium rpm you might need to add 1 degree per 1000 and if all of this is close enough you might need to add 2 degrees of timing per 1000rpm (just example numbers). The point is there are 2 knees in the timing curve and the accuracy of the previous knee effect the results in the subsequent knee. I just go really descriptive about those knees for the sake of understanding. But you could also just set the end bell to handle low rpm, boost to handle mid and turbo to handle high rpm. and if you spend enough time with it you can take a motor that peaks at 150 watts to 300 easily and it will be cooler.
so what happens if the timing isnt right or perfect for that rpm? what happens isnt bad or good. its just something to understand so that you can use it for good or minimize the bad. for every timing point that is not right for an rpm the motor doesnt accelerate as quickly so it doesnt add torque to the next point. secondly the current that should be used to accelerate the motor but cannot be used because the timing isnt right gets turned into heat. the further off the timing is from perfect the more heat. thirdly, because the electrical power moving the rotor isnt right the power that comes back from the motor between pulses isnt right. motors generate electrical power in between the pulses that power the motor. as rpm goes up the electrical power they generate goes higher. at some point the 8.2 volts you are pushing to a motor is matched by 8.2 volts being generated between pulses by the motor and the motor goes no faster. that is max rpm. I had to explain this concept so you can understand what happens when timing isnt right. if the timing isnt right, its said the field is weak. intentionally or accidentally weakening the field is called field weakening. so if the electrical pulse that pushes the rotor forward is weak then the power generated between pulses is weak. so it takes longer for the forward electrical power of 8.2 volts to match the backwards electrical power (generated back emf) and the motor can spin faster. it will do it with least torque but it will spin faster. it will generate more heat but it will spin faster.
so the moral of the story is you never want to weaken the field if you can gear the car and load to match the mechanical power generated with perfect timing. some motors have peak power at 10k some at 15 and some at 20. if you have a track that takes 60 seconds to do a lap you want the average rpm to be at that motors peak rpm. obviously the motor starts at 0 and ends at 20k (example). if the motor constantly accelerates over 60 seconds you want a motor that has perfect timing at 10k and timing that matches. these numbers are exaggerations. the only time you would get something out of field weakening is if your motor has peak power at 10k and you cant gear it to get an average of 12k that the track needs based on its length. in that case you would take away peak power by advancing the timing to weaken the field so that it will average 12k. the only way you get an advantage from field weakening is if you get a wider powerband (not peakier) and this usually only happens if you dont have a motor that has peak power at 12k and you cant get enough gearing into the car to match the average peak power of the motor to match the average peak power the track needs.
a motor manufacturer can give you a set of numbers for that specific motor that takes into account current like 6 amps and a kv number and a timing number that gets you close to that specific motors peak power and you can apply it in a way that minimizes heat and maximizes power but its for a specific motor but you cannot apply it to all motors. every motor has a different resistance. if 1 motor has a different resistance than another then the 8.2 volts going to the motor will match the rpm at which 8.2 volts generated by the motor at a different time and max rpm will be different.
the best way to figure all of this out if you dont have a set of numbers form the mfg and you dont have a dyno is to watch your time per lap. get it as good as you can with gearing. then adjust the timing to minimize heat. if you cant run a race without over heating gear the car to turn 1000 rpm more and adjust the timing again.
every rpm on the curve generates some ratio of torque and heat. the beginning and end of the curve (low and high rpm) generates more heat than mechanical power. bad timing only creates more heat than mechanical power. so you can widen the curve (if that helps) with field weakening or you can use the gearing and timing by lap time to set the motor to the peak power rpm average.
Last edited by Bry195; 04-07-2022 at 08:14 PM.
#32
Tech Regular

Did a project with my son for advanced physics class. We did not race cars to see which is faster, all was done on the bench (so just pure physics, not racing!) We used a Facts Inertia Dyno converted to brushless.
Important findings:
1) Endbell timing marks were off in most motors. Some were way off.
2) Electrical power going into the motor and the work the motor does are measured in the SAME UNITS (1 watt is 0.00135962 horsepower)
3) Most 3 pole motors performed best (tradeoff between heat production and mechanical power) at around 20 to 30 degrees advance.
4) Timing beyond 30 degrees produced excessive heat with not as much gain in mechanical power.
5) Endbell timing alters the mechanical advantage between the stationary and moving magnets. Not unlike the mechanical advantage changes of gearing. Over small changes of each, it is not unreasonable to equate endbell timing changes with gearing changes as they can produce similar effects increasing power to the tires at the expense of heat generation.
6) Due to the deleterious effects of heat on electric motors, most students (that don't race RC cars) were surprised the typical motor construction did not incorporate a cooling mechanism (internal fan or cooling holes).
The diagram below is an example of typical findings for most motors. "Power" on the vertical axis and actual (not indicated) endbell timing on the horizontal axis.
The top curve is the power the motor consumes.
The bottom curve is the power the motor outputs turning the disk.
The difference in the curves is proportional to heat generation due to conservation of energy and matter.
First curves are for a 21.5 and the second one is for a 17.5.
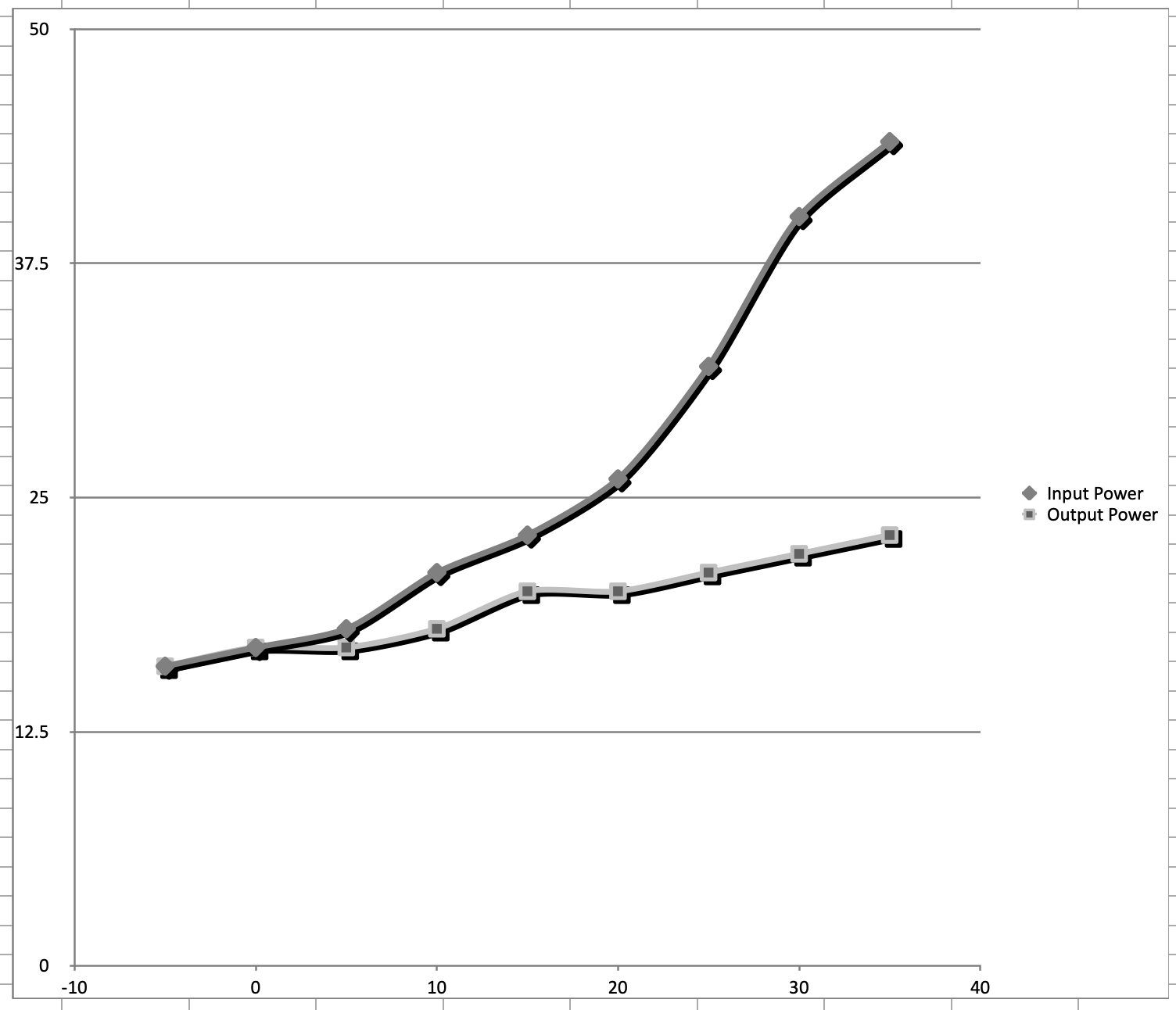
`
Important findings:
1) Endbell timing marks were off in most motors. Some were way off.
2) Electrical power going into the motor and the work the motor does are measured in the SAME UNITS (1 watt is 0.00135962 horsepower)
3) Most 3 pole motors performed best (tradeoff between heat production and mechanical power) at around 20 to 30 degrees advance.
4) Timing beyond 30 degrees produced excessive heat with not as much gain in mechanical power.
5) Endbell timing alters the mechanical advantage between the stationary and moving magnets. Not unlike the mechanical advantage changes of gearing. Over small changes of each, it is not unreasonable to equate endbell timing changes with gearing changes as they can produce similar effects increasing power to the tires at the expense of heat generation.
6) Due to the deleterious effects of heat on electric motors, most students (that don't race RC cars) were surprised the typical motor construction did not incorporate a cooling mechanism (internal fan or cooling holes).
The diagram below is an example of typical findings for most motors. "Power" on the vertical axis and actual (not indicated) endbell timing on the horizontal axis.
The top curve is the power the motor consumes.
The bottom curve is the power the motor outputs turning the disk.
The difference in the curves is proportional to heat generation due to conservation of energy and matter.
First curves are for a 21.5 and the second one is for a 17.5.
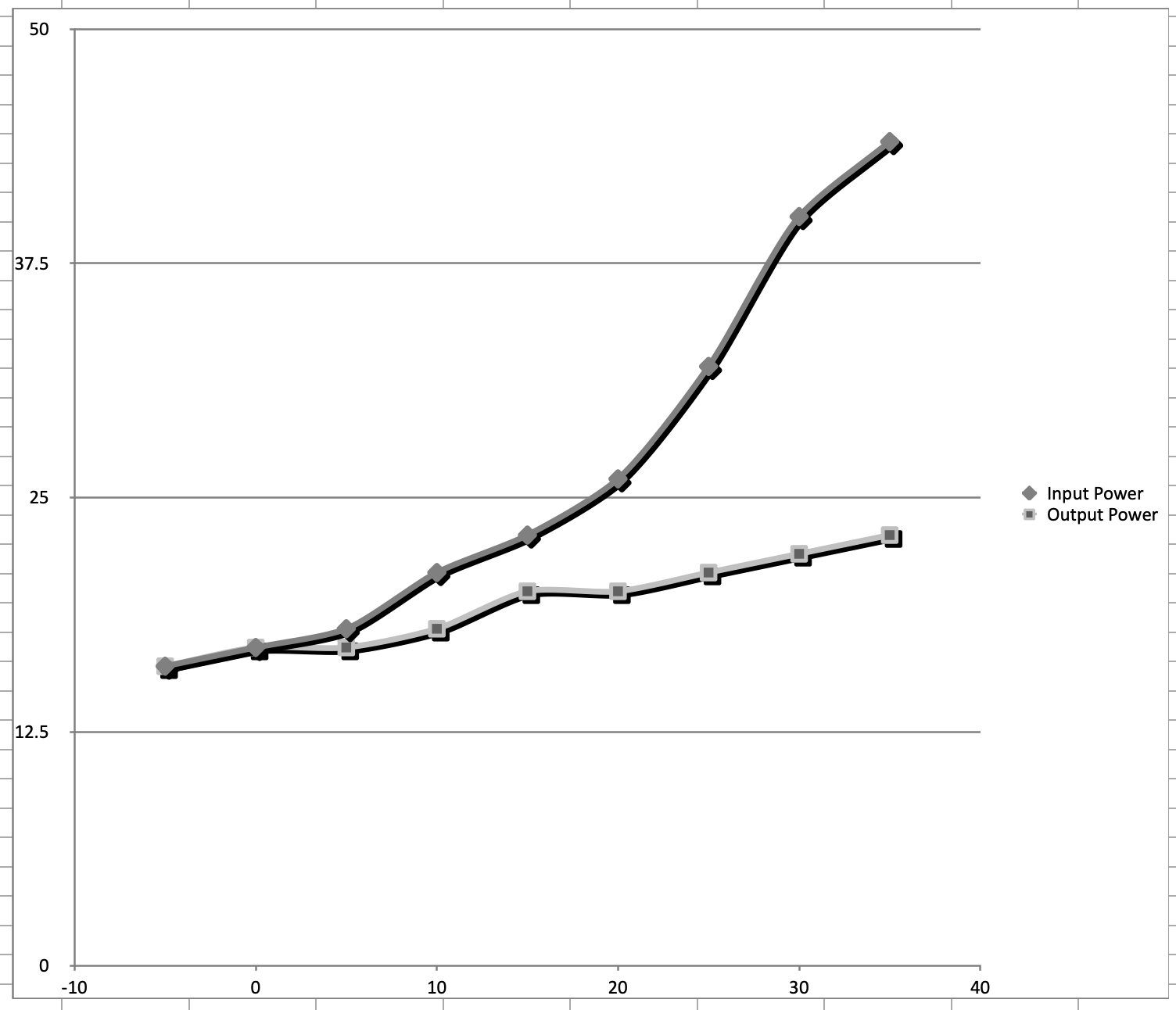
`
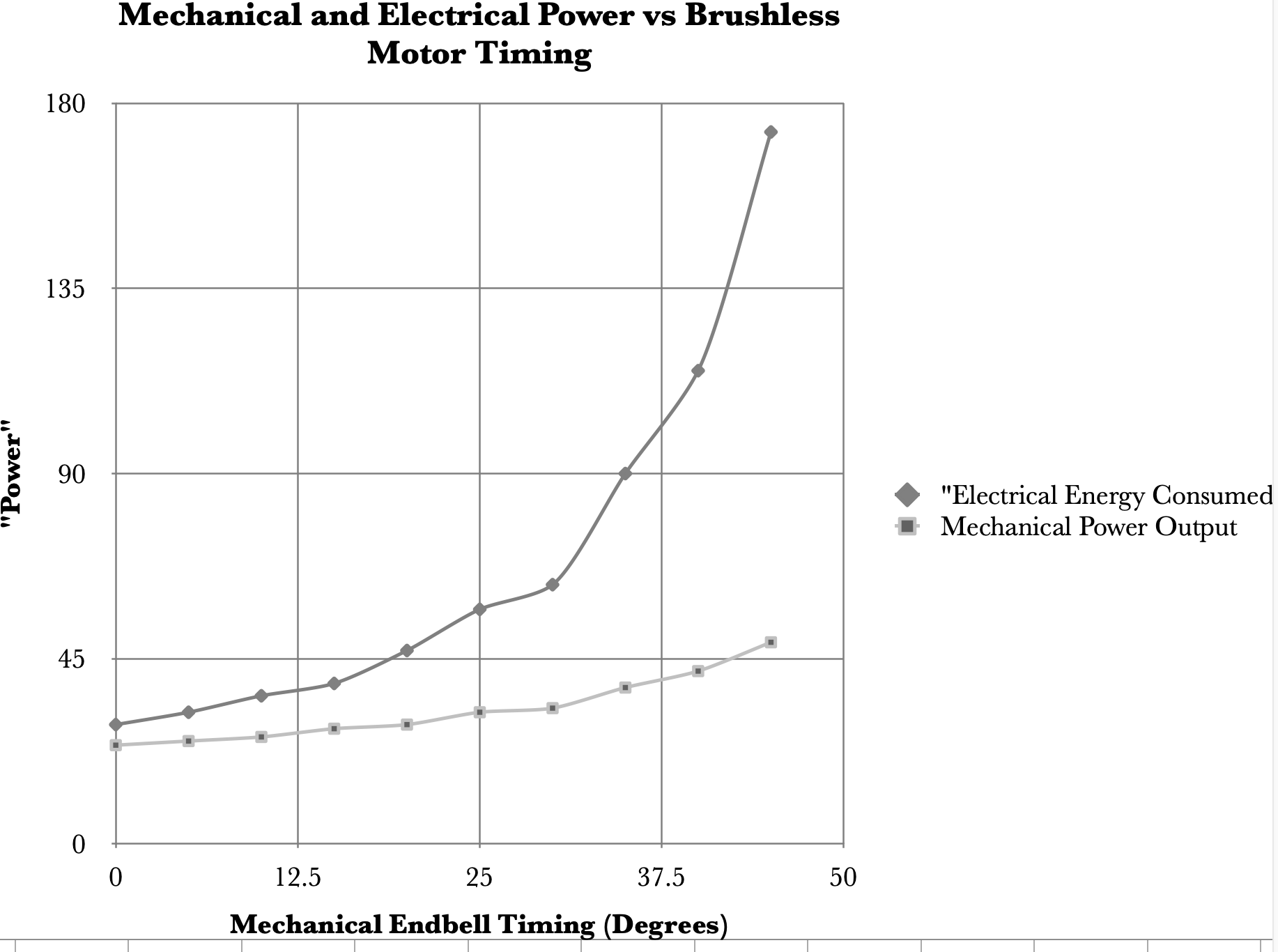
Last edited by ic-racer; 04-08-2022 at 09:52 AM.
#33

the best timing is timing that moves continuously with rpm. there is 1 timing point that generates maximum torque for every rpm. as the rpm goes up or down the timing must do the same if you want peak torque.
so we understand a point on the power curve but there are 20k point on a curve. if if the timing was perfect at 10000 then the motor will be faster at 11000 than it would be if the timing was a little off at 10k. so the previous perfect timing is additive to the next rpm. So the entire 20k points are effected by the previous rpm or the previous timing. so then you might think that you can add .5 degrees per 1000 rpm and that will get you perfect timing. unfortunately it doesnt work that way. at low rpm big changes in timing make very small changes in efficiency. at medium rpm you might need to add 1 degree per 1000 and if all of this is close enough you might need to add 2 degrees of timing per 1000rpm (just example numbers). The point is there are 2 knees in the timing curve and the accuracy of the previous knee effect the results in the subsequent knee. I just go really descriptive about those knees for the sake of understanding. But you could also just set the end bell to handle low rpm, boost to handle mid and turbo to handle high rpm. and if you spend enough time with it you can take a motor that peaks at 150 watts to 300 easily and it will be cooler.
so what happens if the timing isnt right or perfect for that rpm? what happens isnt bad or good. its just something to understand so that you can use it for good or minimize the bad. for every timing point that is not right for an rpm the motor doesnt accelerate as quickly so it doesnt add torque to the next point. secondly the current that should be used to accelerate the motor but cannot be used because the timing isnt right gets turned into heat. the further off the timing is from perfect the more heat. thirdly, because the electrical power moving the rotor isnt right the power that comes back from the motor between pulses isnt right. motors generate electrical power in between the pulses that power the motor. as rpm goes up the electrical power they generate goes higher. at some point the 8.2 volts you are pushing to a motor is matched by 8.2 volts being generated between pulses by the motor and the motor goes no faster. that is max rpm. I had to explain this concept so you can understand what happens when timing isnt right. if the timing isnt right, its said the field is weak. intentionally or accidentally weakening the field is called field weakening. so if the electrical pulse that pushes the rotor forward is weak then the power generated between pulses is weak. so it takes longer for the forward electrical power of 8.2 volts to match the backwards electrical power (generated back emf) and the motor can spin faster. it will do it with least torque but it will spin faster. it will generate more heat but it will spin faster.
so the moral of the story is you never want to weaken the field if you can gear the car and load to match the mechanical power generated with perfect timing. some motors have peak power at 10k some at 15 and some at 20. if you have a track that takes 60 seconds to do a lap you want the average rpm to be at that motors peak rpm. obviously the motor starts at 0 and ends at 20k (example). if the motor constantly accelerates over 60 seconds you want a motor that has perfect timing at 10k and timing that matches. these numbers are exaggerations. the only time you would get something out of field weakening is if your motor has peak power at 10k and you cant gear it to get an average of 12k that the track needs based on its length. in that case you would take away peak power by advancing the timing to weaken the field so that it will average 12k. the only way you get an advantage from field weakening is if you get a wider powerband (not peakier) and this usually only happens if you dont have a motor that has peak power at 12k and you cant get enough gearing into the car to match the average peak power of the motor to match the average peak power the track needs.
a motor manufacturer can give you a set of numbers for that specific motor that takes into account current like 6 amps and a kv number and a timing number that gets you close to that specific motors peak power and you can apply it in a way that minimizes heat and maximizes power but its for a specific motor but you cannot apply it to all motors. every motor has a different resistance. if 1 motor has a different resistance than another then the 8.2 volts going to the motor will match the rpm at which 8.2 volts generated by the motor at a different time and max rpm will be different.
the best way to figure all of this out if you dont have a set of numbers form the mfg and you dont have a dyno is to watch your time per lap. get it as good as you can with gearing. then adjust the timing to minimize heat. if you cant run a race without over heating gear the car to turn 1000 rpm more and adjust the timing again.
every rpm on the curve generates some ratio of torque and heat. the beginning and end of the curve (low and high rpm) generates more heat than mechanical power. bad timing only creates more heat than mechanical power. so you can widen the curve (if that helps) with field weakening or you can use the gearing and timing by lap time to set the motor to the peak power rpm average.
so we understand a point on the power curve but there are 20k point on a curve. if if the timing was perfect at 10000 then the motor will be faster at 11000 than it would be if the timing was a little off at 10k. so the previous perfect timing is additive to the next rpm. So the entire 20k points are effected by the previous rpm or the previous timing. so then you might think that you can add .5 degrees per 1000 rpm and that will get you perfect timing. unfortunately it doesnt work that way. at low rpm big changes in timing make very small changes in efficiency. at medium rpm you might need to add 1 degree per 1000 and if all of this is close enough you might need to add 2 degrees of timing per 1000rpm (just example numbers). The point is there are 2 knees in the timing curve and the accuracy of the previous knee effect the results in the subsequent knee. I just go really descriptive about those knees for the sake of understanding. But you could also just set the end bell to handle low rpm, boost to handle mid and turbo to handle high rpm. and if you spend enough time with it you can take a motor that peaks at 150 watts to 300 easily and it will be cooler.
so what happens if the timing isnt right or perfect for that rpm? what happens isnt bad or good. its just something to understand so that you can use it for good or minimize the bad. for every timing point that is not right for an rpm the motor doesnt accelerate as quickly so it doesnt add torque to the next point. secondly the current that should be used to accelerate the motor but cannot be used because the timing isnt right gets turned into heat. the further off the timing is from perfect the more heat. thirdly, because the electrical power moving the rotor isnt right the power that comes back from the motor between pulses isnt right. motors generate electrical power in between the pulses that power the motor. as rpm goes up the electrical power they generate goes higher. at some point the 8.2 volts you are pushing to a motor is matched by 8.2 volts being generated between pulses by the motor and the motor goes no faster. that is max rpm. I had to explain this concept so you can understand what happens when timing isnt right. if the timing isnt right, its said the field is weak. intentionally or accidentally weakening the field is called field weakening. so if the electrical pulse that pushes the rotor forward is weak then the power generated between pulses is weak. so it takes longer for the forward electrical power of 8.2 volts to match the backwards electrical power (generated back emf) and the motor can spin faster. it will do it with least torque but it will spin faster. it will generate more heat but it will spin faster.
so the moral of the story is you never want to weaken the field if you can gear the car and load to match the mechanical power generated with perfect timing. some motors have peak power at 10k some at 15 and some at 20. if you have a track that takes 60 seconds to do a lap you want the average rpm to be at that motors peak rpm. obviously the motor starts at 0 and ends at 20k (example). if the motor constantly accelerates over 60 seconds you want a motor that has perfect timing at 10k and timing that matches. these numbers are exaggerations. the only time you would get something out of field weakening is if your motor has peak power at 10k and you cant gear it to get an average of 12k that the track needs based on its length. in that case you would take away peak power by advancing the timing to weaken the field so that it will average 12k. the only way you get an advantage from field weakening is if you get a wider powerband (not peakier) and this usually only happens if you dont have a motor that has peak power at 12k and you cant get enough gearing into the car to match the average peak power of the motor to match the average peak power the track needs.
a motor manufacturer can give you a set of numbers for that specific motor that takes into account current like 6 amps and a kv number and a timing number that gets you close to that specific motors peak power and you can apply it in a way that minimizes heat and maximizes power but its for a specific motor but you cannot apply it to all motors. every motor has a different resistance. if 1 motor has a different resistance than another then the 8.2 volts going to the motor will match the rpm at which 8.2 volts generated by the motor at a different time and max rpm will be different.
the best way to figure all of this out if you dont have a set of numbers form the mfg and you dont have a dyno is to watch your time per lap. get it as good as you can with gearing. then adjust the timing to minimize heat. if you cant run a race without over heating gear the car to turn 1000 rpm more and adjust the timing again.
every rpm on the curve generates some ratio of torque and heat. the beginning and end of the curve (low and high rpm) generates more heat than mechanical power. bad timing only creates more heat than mechanical power. so you can widen the curve (if that helps) with field weakening or you can use the gearing and timing by lap time to set the motor to the peak power rpm average.
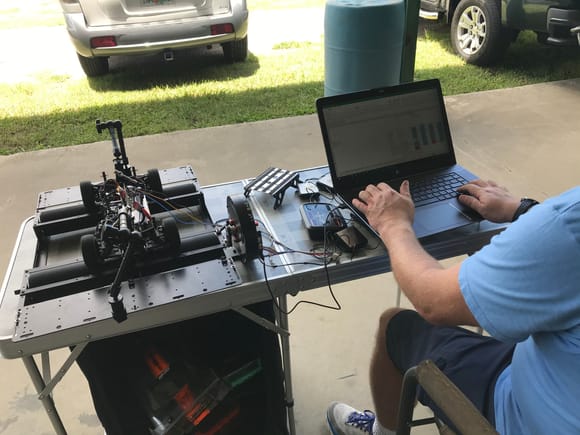
i wonder who that guy is squeezing the most efficient power out of my 17.5

#34

Motor timing is almost an IQ test. Can you learn and follow patterns? Can you tell if something is not running right? If so, please proceed, if not, please refrain from adjusting the timing on your motor.
Its also surprising how differently motors can react to a change in static timing. Some motors run well in the 45-55 degree range, my 17.5 turn Team Powers motor ran 55 degrees in a 1/12 pan car and free-spin only drew about 5 amps, my Orca touring car handout motor would have melted down at that setting, and wanted about 40 degrees of timing for a good blend of performance and low temperatures.
Its also surprising how differently motors can react to a change in static timing. Some motors run well in the 45-55 degree range, my 17.5 turn Team Powers motor ran 55 degrees in a 1/12 pan car and free-spin only drew about 5 amps, my Orca touring car handout motor would have melted down at that setting, and wanted about 40 degrees of timing for a good blend of performance and low temperatures.
#35
Tech Master

In my opinion the esc mfg should eliminate manual timing and let the esc manage it. if motors are regulated by ROAR for resistance and so on then eliminating the errors introduced by people playing with the timing should be done away with. the difference between one motor and another shouldn’t depend on someone’s understanding of timing. if the esc managed timing the difference between one 17.5 and another would be smaller. people wouldn’t have to worry about amps and kv anymore. they would just have to understand that heat is bad and gearing properly balances heat against lap time.
a 21.5 would be as fast as a 17.5 and as cool as a 13.5. racing would be more about understanding the track and driving line.
on a side note Ive explained this average rpm for peak power and adjusting the timing and gearing to the track so that you spend most of your time at peak power to run faster laps. allot of guys like torque motors. motors that produce more power at low rpm. this might be the right motor for guys who understand gearing and roll out but that creates a very narrow band for peak motor power. so much so that on the USGT motor the difference between peak power on a new set of tires versus old set of tires (smaller diameter) is about 2-3 teeth on the pinion gear. a newer racer would be more competitive without as much tinkering if they selected high rpm motors. there is nothing wrong with the usgt motor its just an example of a low rpm motor and the extra knowledge it takes to be competitive.
Last edited by Bry195; 04-08-2022 at 08:26 PM.
#36

In my opinion the esc mfg should eliminate manual timing and let the esc manage it. if motors are regulated by ROAR for resistance and so on then eliminating the errors introduced by people playing with the timing should be done away with. the difference between one motor and another shouldn’t depend on someone’s understanding of timing. if the esc managed timing the difference between one 17.5 and another would be smaller. people wouldn’t have to worry about amps and kv anymore. they would just have to understand that heat is bad and gearing properly balances heat against lap time.
a 21.5 would be as fast as a 17.5 and as cool as a 13.5. racing would be more about understanding the track and driving line.
on a side note Ive explained this average rpm for peak power and adjusting the timing and gearing to the track so that you spend most of your time at peak power to run faster laps. allot of guys like torque motors. motors that produce more power at low rpm. this might be the right motor for guys who understand gearing and roll out but that creates a very narrow band for peak motor power. so much so that on the USGT motor the difference between peak power on a new set of tires versus old set of tires (smaller diameter) is about 2-3 teeth on the pinion gear. a newer racer would be more competitive without as much tinkering if they selected high rpm motors. there is nothing wrong with the usgt motor its just an example of a low rpm motor and the extra knowledge it takes to be competitive.
a 21.5 would be as fast as a 17.5 and as cool as a 13.5. racing would be more about understanding the track and driving line.
on a side note Ive explained this average rpm for peak power and adjusting the timing and gearing to the track so that you spend most of your time at peak power to run faster laps. allot of guys like torque motors. motors that produce more power at low rpm. this might be the right motor for guys who understand gearing and roll out but that creates a very narrow band for peak motor power. so much so that on the USGT motor the difference between peak power on a new set of tires versus old set of tires (smaller diameter) is about 2-3 teeth on the pinion gear. a newer racer would be more competitive without as much tinkering if they selected high rpm motors. there is nothing wrong with the usgt motor its just an example of a low rpm motor and the extra knowledge it takes to be competitive.
#37

Even in sensorless cogging can be eliminated if you start the motor in low rpm just as a normal 3 phase motor w/o any feedback reading of the rotor.
But yes, if a motor analizer could read the timing of each sensor when starting up then an ESC could do it as well. Then it is possible put in any correction on the timing for each sensor to give the whole system a standard timing and an equal timing on each sensor.
But yes, if a motor analizer could read the timing of each sensor when starting up then an ESC could do it as well. Then it is possible put in any correction on the timing for each sensor to give the whole system a standard timing and an equal timing on each sensor.
#38

#39

Some ESCs already support switching to sensorless at higher RPMs. Hobbywing calls it Sensored/Sensorless Hybrid mode, and I think Castle calls it SmartSense. It's not ROAR legal to use that mode in Blinky classes. There isn't a fixed timing correction offset either. The magnetic field distorts as RPM increases, which will change the measured back EMF used by sensorless mode. The ESC simply ignores the motor sensor once a certain RPM is reached and switches to sensorless operation.
#40

It is a one false movement of max a 1/3rd rotation of the motor (with an FDR of 4 already hardly noticeable on the car) when the rotor is in the most wrong position, from there a normal 3 phase system will spin the motor w/o any further stutter. When the rotation speed is good enough so the ESC can read the feedback it can switch over to sensorless mode (= sensored by the motor coils)
I am aware of the option to swtch from sensor to sensorless and indeed it is not allowed to use it. Over here when driving in the rain running sensorless or even a brushed motor (only with F1) is allowed due the issues of water on the sensors with which I also have a prooved solution. But my idea is something new that is possible to use to end all the cheating on shifted sensors in a stock class. Let the ESC look up the sensor timings and set its electronic timing on each sensor with it to an all same timing. Cheating on shifting sensors will not have any use, even shimming the rotor could not make a difference.
#41

The current system with a sensor board has no cogging. What you just described is a regression in performance, racers won't like it. And what do you mean switching over to sensorless mode? The cogging at startup we're discussing here is full sensorless, it doesn't happen with hybrid.
So my idea is program the ESC on low RPM as a simple 3 phase controler w/o reading the rotor position and when enough rpm is reached or enough feedback signal is detected then switching over into the normal brushless sensorless mode.
In this way a sensorless system can start smooth w/o any cogging
But lets say you have a sensor plate locked at 10 degrees and by specs the manufacturer determine the total timing may be 20 degrees. then the ESC is reading the 3 sensors that can be like 9, 10 and 11 degrees so the ESC need to add 11, 10 and 9 degrees to get all sensors at 20 degrees. In that way you get an equal sensor timing every time the ESC is swiched on and the cheaters can try anything but at the end the total timing will still be 20 degrees.
#42

Actually sensorless is a wrong description, also sensorless is sensoring the position of the rotor but done by the coils of the motor. Problem what is causing cogging is that a slow rotating rotor does not build up enough voltage in a coil to get read by the ESC and so the ESC does not know what to do with the next step of controlling the motor, that results in some stutter in the hope it gets one feedback signal to start up the motor.
So my idea is program the ESC on low RPM as a simple 3 phase controler w/o reading the rotor position and when enough rpm is reached or enough feedback signal is detected then switching over into the normal brushless sensorless mode.
In this way a sensorless system can start smooth w/o any cogging
So my idea is program the ESC on low RPM as a simple 3 phase controler w/o reading the rotor position and when enough rpm is reached or enough feedback signal is detected then switching over into the normal brushless sensorless mode.
In this way a sensorless system can start smooth w/o any cogging
Real stock class racing as we in Europ know use a 1 type motor/ESC combo, the used motor has a locked endbell. The chreater still shifts the sensors on the sensor plate or try to fix some room on the endbell to get more sensor timing which is not allowed but hardly detected. That is why the ETS knows a random handout motor.
But lets say you have a sensor plate locked at 10 degrees and by specs the manufacturer determine the total timing may be 20 degrees. then the ESC is reading the 3 sensors that can be like 9, 10 and 11 degrees so the ESC need to add 11, 10 and 9 degrees to get all sensors at 20 degrees. In that way you get an equal sensor timing every time the ESC is swiched on and the cheaters can try anything but at the end the total timing will still be 20 degrees.
But lets say you have a sensor plate locked at 10 degrees and by specs the manufacturer determine the total timing may be 20 degrees. then the ESC is reading the 3 sensors that can be like 9, 10 and 11 degrees so the ESC need to add 11, 10 and 9 degrees to get all sensors at 20 degrees. In that way you get an equal sensor timing every time the ESC is swiched on and the cheaters can try anything but at the end the total timing will still be 20 degrees.
#43

It's called sensorless because there are no dedicated sensors. Cogging with sensorless is mostly caused by firing the wrong phase at low RPM. Sensorless ESCs already don't try to read the position when there's no feedback, and they still stutter and/or have latency. I feel like we're just repeating ourselves on this.
Like I asked before, what's the benefit of doing that vs running sensorless? How safe is it for the ESC to just start spinning the motor for ~5 second or more at full throttle when you turn it on to measure the sensors? Motor analysers need the pinion disconnected. And why would an ESC have a fixed timing offset like that if different motors respond differently to timing? 20 degrees will overheat a lot of motors. Too little timing can lead to poor efficiency too.
#44

Because most racers do not want sensorless and so any attempt of getting it will be voted away. Trying to setup a stock class with a sensorless set will loose drivers because cogging and poor driveabillity is pinned in their minds even with those who never have runned sensorless. But probably it is also the unknown, all drivers know there is a lot to gain with the sensors, legally and illegal. That knowledge or advantage is for sure gone with sensorless.
#45
Tech Master

How would the ESC manufacturer eliminate manual motor timing? The ESC can only respond to the inputs. If the motor is sending through advanced signals, the ESC won't know. The only real way to do that would be to only use the sensor cable for startup to reduce cogging, then dropping to sensorless mode (which violates ROAR rules) once the car is rolling. But then you run into problems where different motors have different optimal timing ranges, so then you run into situations where buying specific brands of motors nets more performance for the timing that the ESC is choosing. And if different ESCs are choosing different timing profiles, then there will be an ESC war again.
control of cogging in our motors can be a little more complicated but there are lots of methods. cogging is caused by a dramatic push and pull between the magnet and the coil. most methods to minimize cogging comes from tapering current in and out of the coil so the jump from the current magnet to the next magnet is more gradual. the electrical wave form for our motors is very square. trapezoidal to be specific. you can simulate a sin wave better than we do now and that would help. you can also angle the magnets so that the transition from one magnet to the next is angled so physically control the transition from north to south more gradually.
an esc mfg can actually use the microprocessor to automatically control timing and keep you from burning up your motor. you have sensors in the motor and its very easy to predict how much heat is in a motor from an acute and chronic perspective. But I would be happy with just auto timing.