Maximising engine characteristics.
#1

Won't postpone this any more. I'll start today and add to the first post when I have time and feeling less ill.
Before being into suspension setup and design I was into engines. Fast forward a few years and since suspension stuff has reached a level I'm good at I returned to engine stuff.
First I have to thank Mr. Faisal Ali for sending the engine.
So, having an EBIS broke in engine as the test subject I can add hands on experience, in this thread I will write about what are the things to change in order to cater the engine to the needs of the driver/track/car.
Introduction:
As you know engines are basically air pumps. Air and fuel is sucked and then hot gases from the combustion are sent down through the exhaust, the more easily they flow the more efficient the engine will be. The losses caused by worse flow conditions are known as pumping/scavenging losses. The more fuel and air you can cram inside the combustion chamber the more powerful will be the combustion cycle provided you can harness that energy efficiently. The things that provide more power are:more mixture in the combustion chamber, more rpm and good flow. Those are the basics.
Carb Tech:
Focusing on two stroke rc engines the physics of the larger engines still apply, being of course limited by manufacturing or design constraints. One thing I would like is standardized parts like carbs, jets and seals. This Reds engine has some cool stuff like the horizontal carb and the offset opening on the venturi. Is the HCX carb better than all the rest? Don't know yet, it's still a two needles on the same jet type. BTW rc airplane engines have the HSN on the back of the engine, away from the propeller, because it doesn't matter HSN placement, it's just a maximum flow valve. The LSN it's a dual purpose flow valve the way it's setup, it has to be have enough flow at idle and thereabouts but allow correct fuel ramping(sort of,as the vacuum sucks what it needs). Long needle vs short needle, horizontal vs normal, offset vs inline I don't think it matters much, if the carb provides the correct amount of fuel to go with the air the piston sucks (and the slide allows) then all is good and the tune method is what can differ. I can be proved wrong, if you have the data then do it. Carb throat I.D. is regulated so you can't cut pumping losses there by going bigger I.D. but there is something working our way. The smaller I.D. will cut the amount of air it can pass through the carb but will increase the air speed, providing better fuel atomization; if the crank has the same smaller I.D. and case volume is small then the mixture will travel faster increasing engine response by arriving faster and displacing exhaust gases sooner (too soon and you start to burn the mixture early or send it with the exhaust gases unburned). You can't expect a different engine to respond the same as another brand engine, catered specifically to smaller venturi I.D. but they will be pretty similar.
Crank and crankcase:
The crank has many roles, starting by the front it's where the clutch assembly rides on then you have something that shouldn't exist that is the inlet window, working as a rotary valve. I haven't seen a normal two stroke engine with something like that, they all inject the mixture directly bellow the piston. They also have reed valves... If there's a limit in making a suitable reed valve and there is a true need to use the crank inlet then I'm cool with it, sub-optimal but understandable. It works by closing and stopping flow for a brief period of time until the piston goes up and creates a pulse of vacuum which will "fetch" the droplets above the inlet once it opens. Those droplets (particularly the oil) can travel to the front bearing if the piston downstroke has enough push to make them travel towards the path of less resistance, hopefully the inlet is closed and that pulse is sent towards the front bearing travelling with some oil. As oil is heavier than the mix it will bump into the backplate and sink into the crankcase where it will sink and provide lubrication for the rear bearing and crank pin. Some will be more atomized and travel upwards hopefully enough to lubricate the piston pin. Slugged cranks have more inertia, slowing down the engine.
Liner and ports:
First misconception, more ports don't provide more power. What matters is port/time area, which is the amount of time the port is open and it's area. Tall ports decrease blowout, which is the expansion of the burning mixture, therefore efficiency. Wider ports increase piston wear and decrease liner durability. That's why having a large port being broken into more smaller ports provide the port/time area the designer choose while providing piston and liner support. A balancing act is critical to achieve high efficiency, wide powerband and good power. Another misconception is that a high revving engine will always be more powerful, not quite. The more rpm the engine is capable of, the more drag the parts will have, either drag from aero or lack of lubrication as the speed is too high for the oil to stay attached to the moving parts and it will start to throw unburned fuel down the exhaust. The rod will be under more stress and will stretch more, calling for lower compression which will reduce efficiency again. So a lower rpm engine, with more and smaller ports, with high compression, good pumping and scavenging will be more efficient and have a wider powerband is what most should look into.
Heat management:
Focusing again on an efficient engine that sips fuel and use it well one starts to get into trouble. The lower amount of fuel will provide less of a cooling effect, needing more heatsink material or the engine being capable of running hotter. Mixture explosion will happen sooner calling for colder plugs. Hotter exhaust gases will travel faster therefore needing a tuned pipe/header change.
That's it for today, next days will measure timings, compression,blowout and others.
Before being into suspension setup and design I was into engines. Fast forward a few years and since suspension stuff has reached a level I'm good at I returned to engine stuff.
First I have to thank Mr. Faisal Ali for sending the engine.
So, having an EBIS broke in engine as the test subject I can add hands on experience, in this thread I will write about what are the things to change in order to cater the engine to the needs of the driver/track/car.
Introduction:
As you know engines are basically air pumps. Air and fuel is sucked and then hot gases from the combustion are sent down through the exhaust, the more easily they flow the more efficient the engine will be. The losses caused by worse flow conditions are known as pumping/scavenging losses. The more fuel and air you can cram inside the combustion chamber the more powerful will be the combustion cycle provided you can harness that energy efficiently. The things that provide more power are:more mixture in the combustion chamber, more rpm and good flow. Those are the basics.
Carb Tech:
Focusing on two stroke rc engines the physics of the larger engines still apply, being of course limited by manufacturing or design constraints. One thing I would like is standardized parts like carbs, jets and seals. This Reds engine has some cool stuff like the horizontal carb and the offset opening on the venturi. Is the HCX carb better than all the rest? Don't know yet, it's still a two needles on the same jet type. BTW rc airplane engines have the HSN on the back of the engine, away from the propeller, because it doesn't matter HSN placement, it's just a maximum flow valve. The LSN it's a dual purpose flow valve the way it's setup, it has to be have enough flow at idle and thereabouts but allow correct fuel ramping(sort of,as the vacuum sucks what it needs). Long needle vs short needle, horizontal vs normal, offset vs inline I don't think it matters much, if the carb provides the correct amount of fuel to go with the air the piston sucks (and the slide allows) then all is good and the tune method is what can differ. I can be proved wrong, if you have the data then do it. Carb throat I.D. is regulated so you can't cut pumping losses there by going bigger I.D. but there is something working our way. The smaller I.D. will cut the amount of air it can pass through the carb but will increase the air speed, providing better fuel atomization; if the crank has the same smaller I.D. and case volume is small then the mixture will travel faster increasing engine response by arriving faster and displacing exhaust gases sooner (too soon and you start to burn the mixture early or send it with the exhaust gases unburned). You can't expect a different engine to respond the same as another brand engine, catered specifically to smaller venturi I.D. but they will be pretty similar.
Crank and crankcase:
The crank has many roles, starting by the front it's where the clutch assembly rides on then you have something that shouldn't exist that is the inlet window, working as a rotary valve. I haven't seen a normal two stroke engine with something like that, they all inject the mixture directly bellow the piston. They also have reed valves... If there's a limit in making a suitable reed valve and there is a true need to use the crank inlet then I'm cool with it, sub-optimal but understandable. It works by closing and stopping flow for a brief period of time until the piston goes up and creates a pulse of vacuum which will "fetch" the droplets above the inlet once it opens. Those droplets (particularly the oil) can travel to the front bearing if the piston downstroke has enough push to make them travel towards the path of less resistance, hopefully the inlet is closed and that pulse is sent towards the front bearing travelling with some oil. As oil is heavier than the mix it will bump into the backplate and sink into the crankcase where it will sink and provide lubrication for the rear bearing and crank pin. Some will be more atomized and travel upwards hopefully enough to lubricate the piston pin. Slugged cranks have more inertia, slowing down the engine.
Liner and ports:
First misconception, more ports don't provide more power. What matters is port/time area, which is the amount of time the port is open and it's area. Tall ports decrease blowout, which is the expansion of the burning mixture, therefore efficiency. Wider ports increase piston wear and decrease liner durability. That's why having a large port being broken into more smaller ports provide the port/time area the designer choose while providing piston and liner support. A balancing act is critical to achieve high efficiency, wide powerband and good power. Another misconception is that a high revving engine will always be more powerful, not quite. The more rpm the engine is capable of, the more drag the parts will have, either drag from aero or lack of lubrication as the speed is too high for the oil to stay attached to the moving parts and it will start to throw unburned fuel down the exhaust. The rod will be under more stress and will stretch more, calling for lower compression which will reduce efficiency again. So a lower rpm engine, with more and smaller ports, with high compression, good pumping and scavenging will be more efficient and have a wider powerband is what most should look into.
Heat management:
Focusing again on an efficient engine that sips fuel and use it well one starts to get into trouble. The lower amount of fuel will provide less of a cooling effect, needing more heatsink material or the engine being capable of running hotter. Mixture explosion will happen sooner calling for colder plugs. Hotter exhaust gases will travel faster therefore needing a tuned pipe/header change.
That's it for today, next days will measure timings, compression,blowout and others.
#3
#4

JP had only a DLC coated crankshaft.
Low friction coatings on pistons (and sleeves) is done a lot as an alternitive for pinching, the coating is the resizing.
So far I know Novarossi had a DLC piston with I believe the Keep-on models
Low friction coatings on pistons (and sleeves) is done a lot as an alternitive for pinching, the coating is the resizing.
So far I know Novarossi had a DLC piston with I believe the Keep-on models
#5

To bad the website is down now, so i can't can't find it to prove it.
#7

i think SH had a ceramic piston as well... not sure how that worked...
#8

There's a company in Russia or the Ukraine that make aircraft engines using a type of ceramic coating on the liner in place of chrome. I forget what the exact compound is. It makes an incredibly long lasting liner, but break-in of said engine takes a long time and you have to use a self grounding glow driver to light the plug because the coating on the liner doesn't conduct electricity.
I'd heard of another fellow that wanted to snug up the piston fit inside the liner - what he chose to do was essentially electroplate the piston with a high silicon aluminum. Anodizing would work too if the fit was tight already.
I'd heard of another fellow that wanted to snug up the piston fit inside the liner - what he chose to do was essentially electroplate the piston with a high silicon aluminum. Anodizing would work too if the fit was tight already.
#10


Sleeve:
The sleeve has 9 transfer ports and an exhaust with booster ports. The piston features a new special black superficial treatment that reduces friction and improves piston strength.
The sleeve has 9 transfer ports and an exhaust with booster ports. The piston features a new special black superficial treatment that reduces friction and improves piston strength.
#12

It's too bad so many engine manufacturers still insist on using brass for their liners instead of aluminum. Aluminum is far more stable and doesn't suffer the same fate that brass does when repeatedly overheated and bell mouths causing a loss of piston seal requiring a re-pinch or replacement of the piston/liner set. With an aluminum liner, you can simply fit a new piston to the old liner and have the same great sealing and performance as it was when new. Some engine manufacturers years ago used to sell oversize pistons to fit into used liners when the fit is lost between the two. One company in particular sold pistons in .00001" increments while another went to .0001" increments.
Nonetheless, I'd like to know how long the coating on these pistons actually lasts. I know most buggy engines made today are nowhere near as tight as they used to be, so maybe that makes the coating last longer..?
Last edited by RCTecher12; 09-06-2017 at 07:22 PM.
#13

It is microns. I have calculated the angle of a Novarossi sleeve and it is about 0.3 degrees. So over a pinch zone of about 4mm in length you can calculate the diameter change.
The tiny spiral on the surface of the piston made by the lathe (can be seen under a magnifier) is basically the break-in surface. If the surface roughness is too high and the starting pinch too low the break in is done very quick but due the left over roughness the piston still wears quickly. When the roughness is too low with a too high pinch the piston surface will be totally flat and then the break in almost stops, a long term high pinch will stay.
See on the left new and on the right the break in.
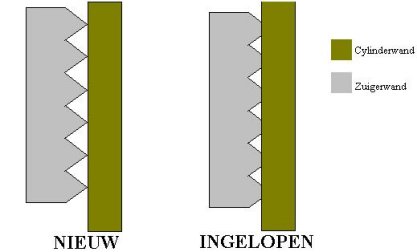
As you see the new tips of the surface it explains why the 1st start must be done carefully so the tips will not burn or break.
I do not share this. As I have assisted the development on an experimental engine with an AAC construction I can tell you that an aluminum sleeve is easily overheated and does expand more than brass. For the most stable engine you want an as low as possible expansion rates for piston and sleeve. As also chrome on aluminum is a difficult process and can come loose. Also be aware the cooling through the head has a huge influence on the expansion of the aluminum sleeve, we had 6 different heads to control the expansion.
But when you get it right it is the better choice, commercial with selling engines around the world to warm and cold places it can become a disaster.
The tiny spiral on the surface of the piston made by the lathe (can be seen under a magnifier) is basically the break-in surface. If the surface roughness is too high and the starting pinch too low the break in is done very quick but due the left over roughness the piston still wears quickly. When the roughness is too low with a too high pinch the piston surface will be totally flat and then the break in almost stops, a long term high pinch will stay.
See on the left new and on the right the break in.
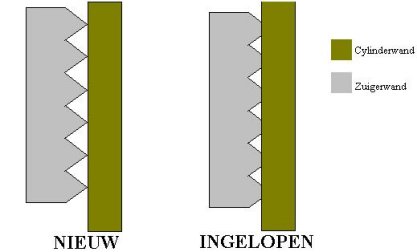
As you see the new tips of the surface it explains why the 1st start must be done carefully so the tips will not burn or break.
It's too bad so many engine manufacturers still insist on using brass for their liners instead of aluminum. Aluminum is far more stable and doesn't suffer the same fate that brass does when repeatedly overheated and bell mouths causing a loss of piston seal requiring a re-pinch or replacement of the piston/liner set. With an aluminum liner, you can simply fit a new piston to the old liner and have the same great sealing and performance as it was when new. Some engine manufacturers years ago used to sell oversize pistons to fit into used liners when the fit is lost between the two. One company in particular sold pistons in .00001" increments while another went to .0001" increments.
But when you get it right it is the better choice, commercial with selling engines around the world to warm and cold places it can become a disaster.
#14

The trick to the aluminum liner and piston combo is getting the alloy correct. No different than brass, the alloy must be correct.
And FWIW - those aircraft engines with aluminum liners and either ceramic coating or chrome; they rarely peel their plating. The components must be plated correctly. Imagine having a bare aluminum liner and an aluminum piston that is hard chrome plated? It works very well in reality as does AAC liners in many many other types of aircraft engines. Nomadic is also used in some as is Nickel, but Nickel is poor for high performance engines. Most of this that I speak of is in regard to aircraft engines. Yes they have a built-in fan for cooling essentially, but they still operate at a higher temperature on average than a buggy engine. I've noted 300-320F in a hard unloaded run on High nitro.
And FWIW - those aircraft engines with aluminum liners and either ceramic coating or chrome; they rarely peel their plating. The components must be plated correctly. Imagine having a bare aluminum liner and an aluminum piston that is hard chrome plated? It works very well in reality as does AAC liners in many many other types of aircraft engines. Nomadic is also used in some as is Nickel, but Nickel is poor for high performance engines. Most of this that I speak of is in regard to aircraft engines. Yes they have a built-in fan for cooling essentially, but they still operate at a higher temperature on average than a buggy engine. I've noted 300-320F in a hard unloaded run on High nitro.
#15
Tech Fanatic

When the roughness is too low with a too high pinch the piston surface will be totally flat and then the break in almost stops, a long term high pinch will stay.
I do not share this. As I have assisted the development on an experimental engine with an AAC construction I can tell you that an aluminum sleeve is easily overheated and does expand more than brass. For the most stable engine you want an as low as possible expansion rates for piston and sleeve. As also chrome on aluminum is a difficult process and can come loose. Also be aware the cooling through the head has a huge influence on the expansion of the aluminum sleeve, we had 6 different heads to control the expansion.
But when you get it right it is the better choice, commercial with selling engines around the world to warm and cold places it can become a disaster.
Though most alloys are like you say, there are brass with less expansion then aluminium, and I do believe that most high end engines use a pretty well matched setup to get as close as possible in expansion rate.
I feel that most ABC engines as well benefits from a good match when it comes too cooling, though they are not as fuzzy as your example.
