Soldering is not easy for me.
#16

Most of the time I do side x side. I only twist if I know that the heat shrink will cover it with no problems. Twisting will probably make a better connection, so would probably be better for power wires.
I think that racers miss some important points about soldering. A proper joint doesn't look like a blob of solder. Remember what conducts electricity better, copper or lead/tin? A big fat shiny blob of solder is basically a resistor inline with your connection. Solder should only be the mechanism that holds the conductors together.
When tinning wires, I make sure that it is properly tinned, then at the last second, I will literally flick the wire to knock off the excess solder. You should be able to see that the wire is made up of individual strands when you do this, however, it should be all bonded together by the tinning process.
When tinning the connector, there should be a thin coating of solder on the connector tab.
When soldering the wires to the connector tab, the solder should form a fillet between the wire and the connector tab, all the way around the wire. By having only the amount of solder on the wire and tab, it will allow you to add just the slightest amount of solder to the joint on final assembly to add in that much needed flux provided in the core of the solder.
I am not against flux. when soldering wires to the tabs of my 4-cell packs, if the solder is giving me a hard time, I will use a dab of flux, or a little touch of fresh solder. I also use flux for assembling new packs.
For general solder jobs, the 40w Weller that your LHS can get (if not, most hardware stores have them) is adequate. For assembling packs, I use the 80 watt Weller that says something about soldering stained glass on the package. It works so quick that the cells are barely warm when fully assembled. For smaller wires, I have a $20 iron I got from RS that works well. However, not needed, but definitely a luxury is the Hakko unit sold under the Hakko name or as a Checkpoint in the LHS. This unit has different tips available to it, and usually comes with the big chisel tip.
Just a note on iron tips... DO NOT GRIND THE TIP TO CLEAN IT. Don't sand it, or file it. I finally have to replace the tip on my Hakko after about 3 years of use, and didn't have to grind it once. The reason is not because of crap stuck to the tip, rather, there is a copper sleeve inside it that is falling apart.
The tip on an iron has a coating, usually a high temp nickel, sometimes something else. Get tip cleaner from RS if you are finding black carbon adhering to the working area of the iron. If you need to get the tip clean right away, sometimes the brass wool from Hakko will do the job nicely. However, things like this aren't always available. I have used the edge of an xacto knife to gently scrape the black soot off the tip before. Think of it as a hygienist scrapes plaque off your teeth. You don't want to damage the nickle coating. Once that is cracked, the pitting and destruction of the tip is only a little time away.
I think that racers miss some important points about soldering. A proper joint doesn't look like a blob of solder. Remember what conducts electricity better, copper or lead/tin? A big fat shiny blob of solder is basically a resistor inline with your connection. Solder should only be the mechanism that holds the conductors together.
When tinning wires, I make sure that it is properly tinned, then at the last second, I will literally flick the wire to knock off the excess solder. You should be able to see that the wire is made up of individual strands when you do this, however, it should be all bonded together by the tinning process.
When tinning the connector, there should be a thin coating of solder on the connector tab.
When soldering the wires to the connector tab, the solder should form a fillet between the wire and the connector tab, all the way around the wire. By having only the amount of solder on the wire and tab, it will allow you to add just the slightest amount of solder to the joint on final assembly to add in that much needed flux provided in the core of the solder.
I am not against flux. when soldering wires to the tabs of my 4-cell packs, if the solder is giving me a hard time, I will use a dab of flux, or a little touch of fresh solder. I also use flux for assembling new packs.
For general solder jobs, the 40w Weller that your LHS can get (if not, most hardware stores have them) is adequate. For assembling packs, I use the 80 watt Weller that says something about soldering stained glass on the package. It works so quick that the cells are barely warm when fully assembled. For smaller wires, I have a $20 iron I got from RS that works well. However, not needed, but definitely a luxury is the Hakko unit sold under the Hakko name or as a Checkpoint in the LHS. This unit has different tips available to it, and usually comes with the big chisel tip.
Just a note on iron tips... DO NOT GRIND THE TIP TO CLEAN IT. Don't sand it, or file it. I finally have to replace the tip on my Hakko after about 3 years of use, and didn't have to grind it once. The reason is not because of crap stuck to the tip, rather, there is a copper sleeve inside it that is falling apart.
The tip on an iron has a coating, usually a high temp nickel, sometimes something else. Get tip cleaner from RS if you are finding black carbon adhering to the working area of the iron. If you need to get the tip clean right away, sometimes the brass wool from Hakko will do the job nicely. However, things like this aren't always available. I have used the edge of an xacto knife to gently scrape the black soot off the tip before. Think of it as a hygienist scrapes plaque off your teeth. You don't want to damage the nickle coating. Once that is cracked, the pitting and destruction of the tip is only a little time away.
#17

Flux is absolutely not needed if you do it right the first time...
If you do use flux, make sure its electrical safe or it will corrode over time. Rosin core solder has some flux in it which is more than enough.
I recommend 60/40 tin/pb solder, it seems to flow the best and always hold.
The best advice I can give is to keep the iron hot, put solder on both pieces (tab and wire or wire and wire) set together, touch soldering iron and let it flow.
I'd post my work, but I'm not going to get a camera just to show my soldering skillz
, I learned how to solder working on PCBs doing mod chips and such, try doing one of the 30+ wire ps2 installs back in the day :-/.
edit: and +1 for not grinding the tip, what he said is correct replace it if its gone through the plating.
If you do use flux, make sure its electrical safe or it will corrode over time. Rosin core solder has some flux in it which is more than enough.
I recommend 60/40 tin/pb solder, it seems to flow the best and always hold.
The best advice I can give is to keep the iron hot, put solder on both pieces (tab and wire or wire and wire) set together, touch soldering iron and let it flow.
I'd post my work, but I'm not going to get a camera just to show my soldering skillz

edit: and +1 for not grinding the tip, what he said is correct replace it if its gone through the plating.
#19

+1 on Twotone
If the tip is already rutted out, go ahead and grind it, you can't hurt worse what is already hurt... But if it is only covered with hard black scale and the plating is still intact, use the brass wool or tip cleaner or lightly scrape it with the xacto if that won't work. But try to maintain the plating, that is what is keeping the tip from rotting away. If it is rotted, it transfers heat less reliably, so when you can, replace the tip.
If the tip is already rutted out, go ahead and grind it, you can't hurt worse what is already hurt... But if it is only covered with hard black scale and the plating is still intact, use the brass wool or tip cleaner or lightly scrape it with the xacto if that won't work. But try to maintain the plating, that is what is keeping the tip from rotting away. If it is rotted, it transfers heat less reliably, so when you can, replace the tip.
#20

It's not missing, it's mentioned as not necessary.
Nope, you don't need it. As I explained earlier it's just a bad idea or at best snake-oil type idea (if it doesn't hurt, it certainly doesn't help at all, so it's just money wasted). And yes, I have tested a number of fluxes. If you can't do it without the flux (i.e. the flux core in the soldering wire is not enough for you) you're not doing it right.
That is simply not true. The flux melts way sooner than the solder because the solder conducts heat and melts it inside, so by the time the solder is melting, the flux is already out. Besides, this is what flux does, lowers the melting temperature of the solder, and homogenises the temperature throughout the molten drop, so the metal is pulled by surface tension into a neat sphere around the joint.
Nope, you don't need it. As I explained earlier it's just a bad idea or at best snake-oil type idea (if it doesn't hurt, it certainly doesn't help at all, so it's just money wasted). And yes, I have tested a number of fluxes. If you can't do it without the flux (i.e. the flux core in the soldering wire is not enough for you) you're not doing it right.
That is simply not true. The flux melts way sooner than the solder because the solder conducts heat and melts it inside, so by the time the solder is melting, the flux is already out. Besides, this is what flux does, lowers the melting temperature of the solder, and homogenises the temperature throughout the molten drop, so the metal is pulled by surface tension into a neat sphere around the joint.
If you are relying on the flux in the core of the solder, you will usually end up with too much solder on the joint.
Thank you all very much for all the helpful tips!
I think the solder I have is rosin-core...
What do you guys do when you are splicing wires together?
1. stack 'em side by side.
2. interlock them like you hold your hands with alternating fingers(???)
3. twist them together.
I think the solder I have is rosin-core...
What do you guys do when you are splicing wires together?
1. stack 'em side by side.
2. interlock them like you hold your hands with alternating fingers(???)
3. twist them together.
I'll say again: Depends on what your criteria for "necessary" is and what you consider an acceptable solder joint.
Here are what I consider acceptable solder joints, done with the addition of flux at every stage:
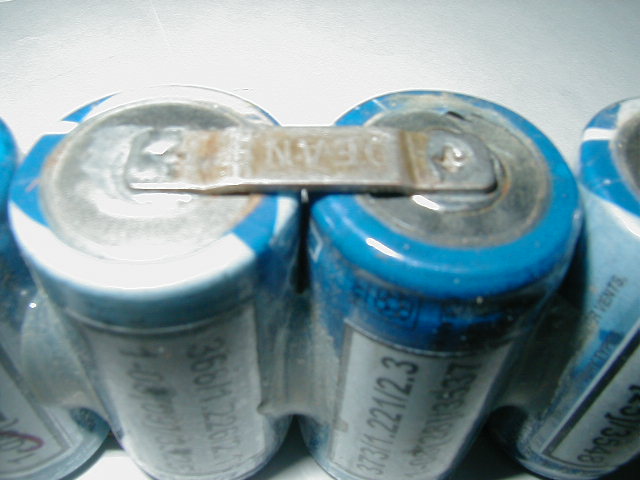
I'd say the joint on the minus side of the bar has a wee bit more solder than was actually needed.

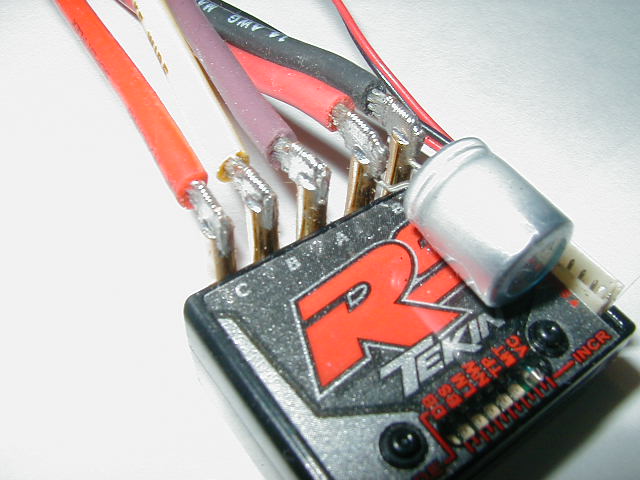
If this had been attempted without flux, they would have ended up requiring much more solder on the iron to get the joint heated up enough for the solder to flow. Any amount of solder more than is required to make the electrical connection is too much. Solder is not a structural material.
Last edited by ta_man; 03-10-2009 at 02:13 PM.
#21
Suspended

Flux allows solder to flower quicker and with less heat needed to melt or transfer the solder.
Flux also is an acid, and it cleans the surfaces of metals to be attached together.
Flux also allows you to make a proper joint without a lot of solder.
While some guys get away without it by using highpowered irons, it's only the extreme heat they're using that allows them to get by with what they're doing. And almost every time I can spot their work by the cold solder joints they produce without knowing it.
I have never had a solder joint fail in which I've used flux, but I've seen hundreds that failed in which flux wasn't used.
#22

Impressive soldering ta-man. I don't use flux so my jobs are a bit messier.
#23

Flux really helps. I'm using the LRP solder station, and its the one thing that I really need more of, I can't keep taking them from school
Plus, it is impossible to get lead solder here. But at school, somehow they get the lead solder so I got a reel of it


#24

As mentioned before, flux is present in the solder wire. And no, that flux is not acid or basic for that matter. It is a product of turpentine refining (colophonium), and it's enough. If you really want to use extra flux, go buy it in a musical instrument shop. They use the same material to make violin strings screech better.
And it's not there for cleaning surfaces. Acid (or alkaline - aka basic) flux does that with the negative consequences I mentioned above. You should steer well clear of these. The surfaces to be soldered should be clean beforehand (and most of the things we talk about here are. It's a different story when you're rewiring a 40 year old real car).
Colophonium is there to lower the melting temperature of the alloy used as solder and the side (desired) efect is it homogenises the temperature creating a blob of solder with the same temperature throughout its mass, therefore capable to adhere equally to everything it comes in contact with.
And yes, I do the "flick the wire" thing too. When I have too much solder I actually blow with my mouth short and very powerful, in a sudden burst. This blows away any excess tin and cools the joint instantly (sure, you can buy "freeze" cans, vacuum pumps and so on, but as I said, I am old skool). My technique is good enough that I don't need a vacuum pump to extract multipin ICs from the pcb they're stuck on.
About splicing, when talking about multiwire strands such as the power wires (with a lot of tiny little wires) I just ruffle them up a bit, then just push the ends into each other, compress by finger as much as I can, solder, then compress round as much as I can without overdoing it in a vice and resolder it, getting rid of a lot of solder in the process. The end result should only be a tad thicker than the original wires themselves. Note, this is one instance where tinning the wires before soldering would not work.
Sure, you don't need a blob of solder, that's true.
But I have to take issue with the rest. If this were the case, they wouldn't bother using solder with better and better conductive properties (silver-enriched, and so on). Copper, silver, etc., do indeed conduct electricity better than tin, lead, etc., but air doesn't. And that's what you're going to have in between your wires, tabs, etc, if not solder. Direct contact between wires is a myth. If you have ever looked at soldering joints under a microscope or on a microelectron probe you'll see. These microgaps are interstellar distances on the atom/electron scale. Try looking such images up on the web.
Or of course, you could try spotwelding everything to everything else, but I am not sure how you'd weld copper to brass or whatever else (and am pretty sure the end result would be worse if only for the limited cross section of the spotwelds).
About our friend's pictures above, they are indeed impressive, but I still argue you don't need extra flux. You would probably win a soldering beauty contest but for functionality, I am not sure your soldering is any better than anyone else's (if they have a bit of skill). As I said before, you invested a lot of money and time in what is essentially just beauty (not a bad thing at all, but beyond my "functionality is all you need" phylosophy). And yes, I produce similar soldering joints without using flux, and no, they don't fail. Do it right, keep it simple. And one suggestion. I would have cut the protruding ends of the wires with a side cutter (look at the terminals where the capacitor is attached). Anyhting to get rid of some useless weight.
About grinding tips, what can I say? I am el cheapo, my soldering iron tips are only retired when they don't exist anymore, hehehehe! But it's true, once the nickel or whatever the protective coating is gone, it's all downhill from there. My tips however last pretty long before they need to be ground, and I am pretty sure if I wasn't using the same tip for other wiring jobs on my real cars, they wouldn't need grinding.
And it's not there for cleaning surfaces. Acid (or alkaline - aka basic) flux does that with the negative consequences I mentioned above. You should steer well clear of these. The surfaces to be soldered should be clean beforehand (and most of the things we talk about here are. It's a different story when you're rewiring a 40 year old real car).
Colophonium is there to lower the melting temperature of the alloy used as solder and the side (desired) efect is it homogenises the temperature creating a blob of solder with the same temperature throughout its mass, therefore capable to adhere equally to everything it comes in contact with.
And yes, I do the "flick the wire" thing too. When I have too much solder I actually blow with my mouth short and very powerful, in a sudden burst. This blows away any excess tin and cools the joint instantly (sure, you can buy "freeze" cans, vacuum pumps and so on, but as I said, I am old skool). My technique is good enough that I don't need a vacuum pump to extract multipin ICs from the pcb they're stuck on.
About splicing, when talking about multiwire strands such as the power wires (with a lot of tiny little wires) I just ruffle them up a bit, then just push the ends into each other, compress by finger as much as I can, solder, then compress round as much as I can without overdoing it in a vice and resolder it, getting rid of a lot of solder in the process. The end result should only be a tad thicker than the original wires themselves. Note, this is one instance where tinning the wires before soldering would not work.
I think that racers miss some important points about soldering. A proper joint doesn't look like a blob of solder. Remember what conducts electricity better, copper or lead/tin? A big fat shiny blob of solder is basically a resistor inline with your connection. Solder should only be the mechanism that holds the conductors together.
But I have to take issue with the rest. If this were the case, they wouldn't bother using solder with better and better conductive properties (silver-enriched, and so on). Copper, silver, etc., do indeed conduct electricity better than tin, lead, etc., but air doesn't. And that's what you're going to have in between your wires, tabs, etc, if not solder. Direct contact between wires is a myth. If you have ever looked at soldering joints under a microscope or on a microelectron probe you'll see. These microgaps are interstellar distances on the atom/electron scale. Try looking such images up on the web.
Or of course, you could try spotwelding everything to everything else, but I am not sure how you'd weld copper to brass or whatever else (and am pretty sure the end result would be worse if only for the limited cross section of the spotwelds).
About our friend's pictures above, they are indeed impressive, but I still argue you don't need extra flux. You would probably win a soldering beauty contest but for functionality, I am not sure your soldering is any better than anyone else's (if they have a bit of skill). As I said before, you invested a lot of money and time in what is essentially just beauty (not a bad thing at all, but beyond my "functionality is all you need" phylosophy). And yes, I produce similar soldering joints without using flux, and no, they don't fail. Do it right, keep it simple. And one suggestion. I would have cut the protruding ends of the wires with a side cutter (look at the terminals where the capacitor is attached). Anyhting to get rid of some useless weight.
About grinding tips, what can I say? I am el cheapo, my soldering iron tips are only retired when they don't exist anymore, hehehehe! But it's true, once the nickel or whatever the protective coating is gone, it's all downhill from there. My tips however last pretty long before they need to be ground, and I am pretty sure if I wasn't using the same tip for other wiring jobs on my real cars, they wouldn't need grinding.
Last edited by niznai; 03-11-2009 at 01:33 AM.
#25
Tech Master
iTrader: (16)

A hint when splicing wires together: Tin the end of each wire (assume we are talking multi-stranded wire) and after the ends are tinned, flatten them partway in a vise, then you can solder the flattened ends together side by side (on the flat parts) and you will get a better joint which takes up less room.
This method puts the copper strands as close together and the solder is just there to hold the wires in place.
Flux's (USE WATER BASED ONLY FOR ELECTRONIC'S)
My solder if choice is AQUALINE (WATER BASED FLUX ,ELECTRONIC's SAFE , LOW TEMP SILVER SOLDER AND EASY TO USE and contains no LEAD

Better replace the wires on that battery pack on that f103 looking like a fire starter someday real soon.

I am a ASE Certified Master Tech and automotive Electronic's Technition By trade. And been doing so for over 22years.
OK my english sucks ,just like my doctors

#26
Suspended

"In high-temperature metal joining processes (welding, brazing and soldering), the primary purpose of flux is to prevent oxidation of the base and filler materials. Tin-lead solder (e.g.) attaches very well to copper, but poorly to the various oxides of copper, which form quickly at soldering temperatures. Flux is a substance which is nearly inert at room temperature, but which becomes strongly reducing at elevated temperatures, preventing the formation of metal oxides. Additionally, flux allows solder to flow easily on the working piece rather than forming beads as it would otherwise."
While some people appear to get by without using it because they feel rosin-core solder fills the need, the long and short of it is that using flux allows one to use less heat and/or produce a usable solder joint faster. Heat is our enemy in RC, as well as the enemy of these micro electronics we use in our hobby.
Standard, off the shelf, rosin-core might be fine for soldering a couple of wires back together on your Buick - but in our case applying heat and waiting several seconds for the rosin to bubble enough that it impregnates the wires and allowing the solder to flow into we're attempting to solder together is not a good thing.
Applying flux drastically cuts this heating time down to milliseconds, allowing a solder joint to be produced in a second or two versus the 10 or 15 seconds or more neccessary for those not using flux.
Last edited by Lightin'; 03-11-2009 at 07:51 AM.
#27
Suspended

Another thing that hasn't been considered is that generally speaking rosin-core solder is the lowest temperature solder sold commercially. This is solder with the lowest possible melting point. While fine for low temperature and low stress applications, like soldering two wires back together in your Buick in the garage, it is not used in all applications in which the items are subjected to high temperatures or submitted to high stresses or impacts.
Can you say RC???
Hereby where silver solder comes in, which has a higher melting temp as well as being harder and producng a tougher solder joint.
It's used by jewelers to solder clasps to chains, and it's also sold in hardware stores right in the soldering section but is easily overlooked.
Has anyone had a solderjoint they produced a while back that was beautiful initially, but much later had the wire break well up the wire from the initial joint? And upon examination found that the wire itself is stiff or harder well up the wire inside the insulation?
This is as a result of the solder "creeping" along the wire over time.
This is also a result of using low temperature solder being used.
The cure for this would be to use silver solder, that will not creep up a wire as almost any electronic curcuit will not produce enough temperature to minutely melt silver and allow it to creep up the wire over time.
This is perfect for any of us building our own battery packs, as it will not get hot enough to heat up and melt during the running of our cars (and popping a battery bar loose from impact or a hard hit during competition), or those of us attaching wires to a ESC in which we are trying to produce a perfect one-time-only solder joint to posts or a curcuit board where the highest heat is produced routinely during the routine operation of our cars each time we run them (you know, motor or battery wires that get hot).
Silver solder does not usually come in the rosin-core variety, but instead as solid wire, and thus needs flux to use it properly.
Can you say RC???
Hereby where silver solder comes in, which has a higher melting temp as well as being harder and producng a tougher solder joint.
It's used by jewelers to solder clasps to chains, and it's also sold in hardware stores right in the soldering section but is easily overlooked.
Has anyone had a solderjoint they produced a while back that was beautiful initially, but much later had the wire break well up the wire from the initial joint? And upon examination found that the wire itself is stiff or harder well up the wire inside the insulation?
This is as a result of the solder "creeping" along the wire over time.
This is also a result of using low temperature solder being used.
The cure for this would be to use silver solder, that will not creep up a wire as almost any electronic curcuit will not produce enough temperature to minutely melt silver and allow it to creep up the wire over time.
This is perfect for any of us building our own battery packs, as it will not get hot enough to heat up and melt during the running of our cars (and popping a battery bar loose from impact or a hard hit during competition), or those of us attaching wires to a ESC in which we are trying to produce a perfect one-time-only solder joint to posts or a curcuit board where the highest heat is produced routinely during the routine operation of our cars each time we run them (you know, motor or battery wires that get hot).
Silver solder does not usually come in the rosin-core variety, but instead as solid wire, and thus needs flux to use it properly.

#28

It appears you are mistaken http://en.wikipedia.org/wiki/Soldering_flux "Flux is corrosive"
"In high-temperature metal joining processes (welding, brazing and soldering), the primary purpose of flux is to prevent oxidation of the base and filler materials. Tin-lead solder (e.g.) attaches very well to copper, but poorly to the various oxides of copper, which form quickly at soldering temperatures. Flux is a substance which is nearly inert at room temperature, but which becomes strongly reducing at elevated temperatures, preventing the formation of metal oxides. Additionally, flux allows solder to flow easily on the working piece rather than forming beads as it would otherwise."
"In high-temperature metal joining processes (welding, brazing and soldering), the primary purpose of flux is to prevent oxidation of the base and filler materials. Tin-lead solder (e.g.) attaches very well to copper, but poorly to the various oxides of copper, which form quickly at soldering temperatures. Flux is a substance which is nearly inert at room temperature, but which becomes strongly reducing at elevated temperatures, preventing the formation of metal oxides. Additionally, flux allows solder to flow easily on the working piece rather than forming beads as it would otherwise."
And about silver solder you're just wrong. I have in my hot little hands a roll of lead-free rosin core solder. According to its label it contains copper, tin and silver!
And about using low temperature solder, I have seen indeed joints coming apart in races, but as they were not mine I can not comment what was going on there but I suspect if your wires go over 190 C (60/40 Sn/Pb melts around 190 C) then the solder you use is the least of your worries.
Good luck
Last edited by niznai; 03-11-2009 at 10:03 AM.
#29
Suspended

That's the problem with wikipedia. It gives people the feeling they know something about err.... something. You can only learn so much on wikipedia as teh writers themselves know. Flux is anything used to lower the melting point of something. This is the most general sense. Which fits here. The problem is people will sell you things which are called "flux" even though their role is somewhat different. Flux is not supposed to clean anything for instance. Oh well, some manufacturers feel it is. Which is why they use all sorts of corrosive addictives in what they sell you as flux. Use at your own peril. Or just for the heck of it take it to the lab to have it analysed.
And about silver solder you're just wrong. I have in my hot little hands a roll of lead-free rosin core solder. According to its label it contains copper, tin and silver!
And about using low temperature solder, I have seen indeed joints coming apart in races, but as they were not mine I can not comment what was going on there but I suspect if your wires go over 190 C (60/40 Sn/Pb melts around 190 C) then the solder you use is the least of your worries.
Good luck
And about silver solder you're just wrong. I have in my hot little hands a roll of lead-free rosin core solder. According to its label it contains copper, tin and silver!
And about using low temperature solder, I have seen indeed joints coming apart in races, but as they were not mine I can not comment what was going on there but I suspect if your wires go over 190 C (60/40 Sn/Pb melts around 190 C) then the solder you use is the least of your worries.
Good luck
No, the only problem with wikipedia is like any other form of reference material is that some people use it to further their knowledge and others are just in denial about anything put in print. I just posted the link hoping you'd pick up something you didn't think you already were an expert about. This whole discussion reminds me of the expression, "smart people learn something new every day, dumb people don't and keep repeating the same old information they thought they knew."
Next time you're in the hardware store or looking at a selection of solder, maybe you should compare the labels and see what the actual content percentages are of the different solders sold commercially. You might be surprised to find that they roll you're currently holding of 60/40 is pretty low temp comparatively and has a very low silver content.
But you're the expert, I was just trying to help.
#30
Tech Regular
iTrader: (18)

No, the only problem with wikipedia is like any other form of reference material is that some people use it to further their knowledge and others are just in denial about anything put in print. I just posted the link hoping you'd pick up something you didn't think you already were an expert about. This whole discussion reminds me of the expression, "smart people learn something new every day, dumb people don't and keep repeating the same old information they thought they knew."
Next time you're in the hardware store or looking at a selection of solder, maybe you should compare the labels and see what the actual content percentages are of the different solders sold commercially. You might be surprised to find that they roll you're currently holding of 60/40 is pretty low temp comparatively and has a very low silver content.
But you're the expert, I was just trying to help.
Next time you're in the hardware store or looking at a selection of solder, maybe you should compare the labels and see what the actual content percentages are of the different solders sold commercially. You might be surprised to find that they roll you're currently holding of 60/40 is pretty low temp comparatively and has a very low silver content.
But you're the expert, I was just trying to help.